PLC Cycle Time
The PLC cycle time determines the program’s repetition frequency. This time is not deterministic. This means that the PLC cycle time can become longer in some programs, and can exceed the cycle time that has been set. If the program requires less time than has been set, it is repeated within the set cycle time, and the remaining duration is padded with background time.
The processing of the Ethernet and the serial interface runs in the background time. This should be set to somewhere between 20 and 50 % of the PLC cycle time.
The mean cycle time is measured in order to optimize the system. You will find this in PLC Control under the Online/Coupler menu item. About 50 % is added to the time determined there, and the result entered as the PLC cycle time. Set the background time to between 20 and 50 % of the PLC cycle time.
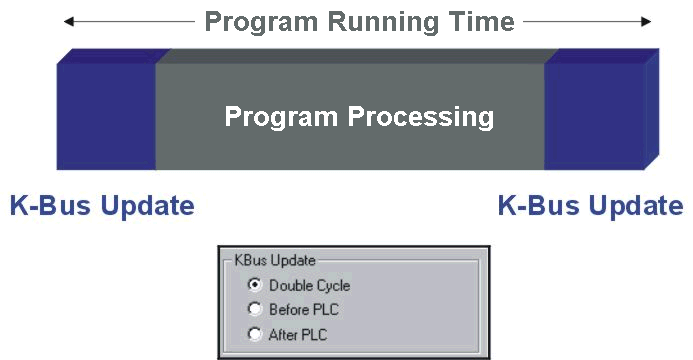
The program running time is composed of the program processing and the K-Bus time. Before the program is called, the Bus Terminal Controller carries out a K-bus update, and reads the current inputs. Following the processing of the program, a second K-bus update takes place in order to write the outputs. The K-Bus time depends on the number and type of Bus Terminals inserted.
The program running time can be shortened by operating only one K-Bus cycle, and this may either be done before or after program processing. In that case, inputs are read and outputs written in a single K-Bus cycle. You can make these settings either with the aid of the KS2000 configuration software, or through ADS.
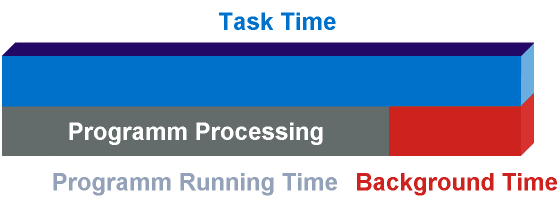