Commissioning the AX8820
The AX8820 universal regenerative unit can be integrated into both an AX5000 system and an AX8000 system. It cannot be integrated into several DC links.
Like other Beckhoff products, it is configured in the TwinCAT 3 XAE development environment and requires an EtherCAT connection. The AX8820 is fully functional if the EtherCAT connection is interrupted. The parameter settings are also saved in the EEPROM of the AX8820 by activating a configuration.
The AX8820 can also be operated as a stand-alone device with the default settings without further configuration.
Default settings
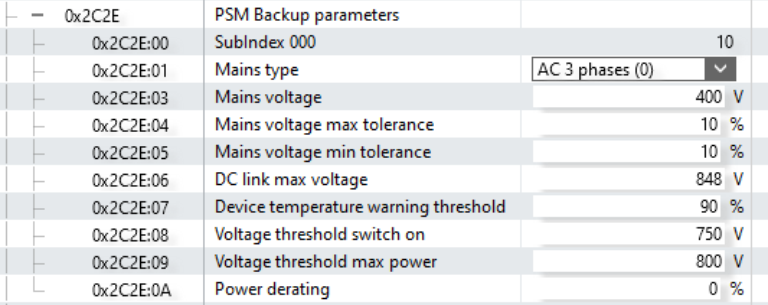
The default settings can be found in the PSM Backup parameters object and are stored in the device's EEPROM. They are used in stand-alone operation. These parameters can only be changed in PreOp mode.
Configuration in TwinCAT
The following instructions describe the configuration in TwinCAT for commissioning the AX8820 with an AX5000. Proceed as follows:
- ►Establish an EtherCAT connection to the AX8820
- ►Create a project in the Solution Explorer or open an existing project
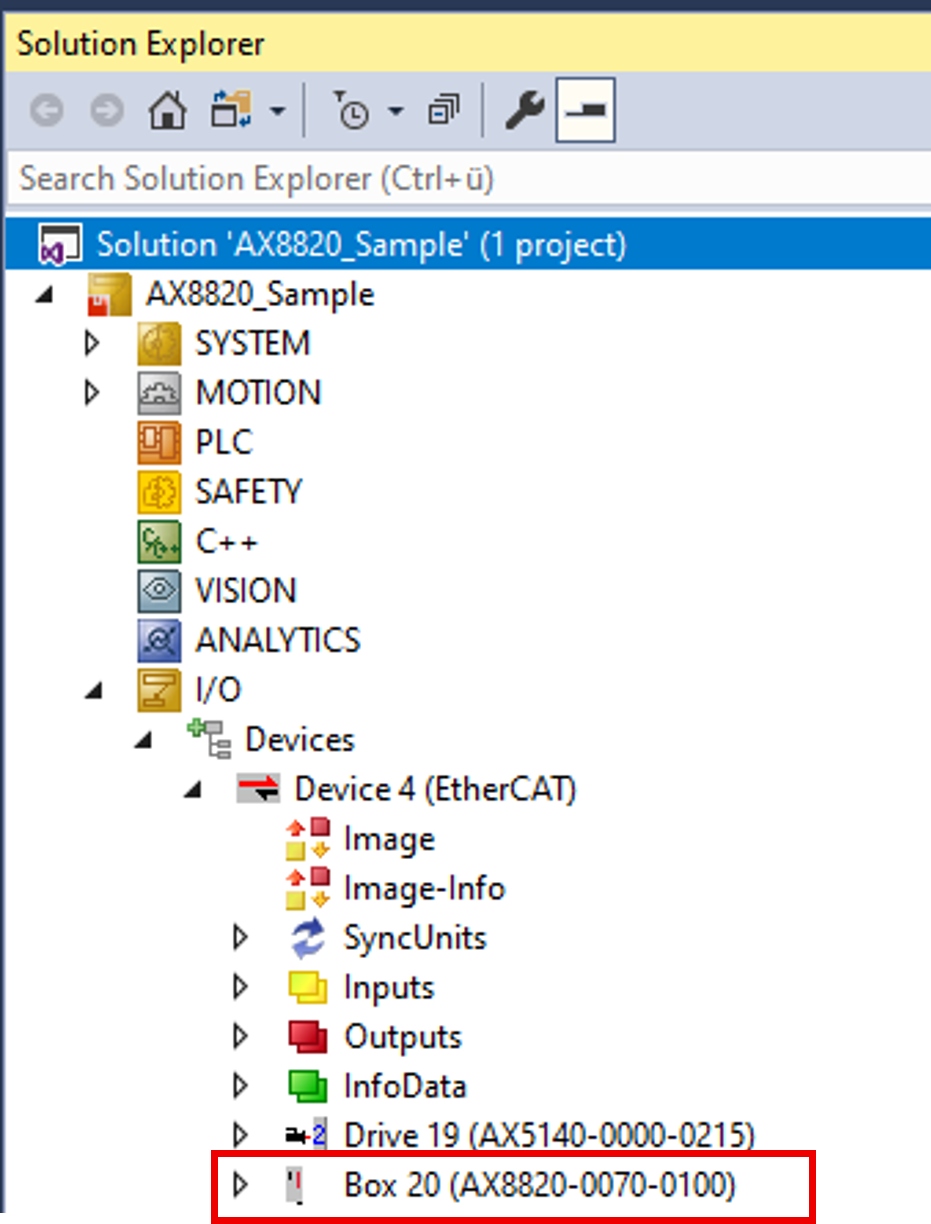
A scan automatically finds the AX8820 when EtherCAT communication is established and adds it to the project. Alternatively, you can add the AX8820 manually when EtherCAT communication is established.
- ►Perform a scan
or
- ►Manually add the AX8820 to the I/O configuration
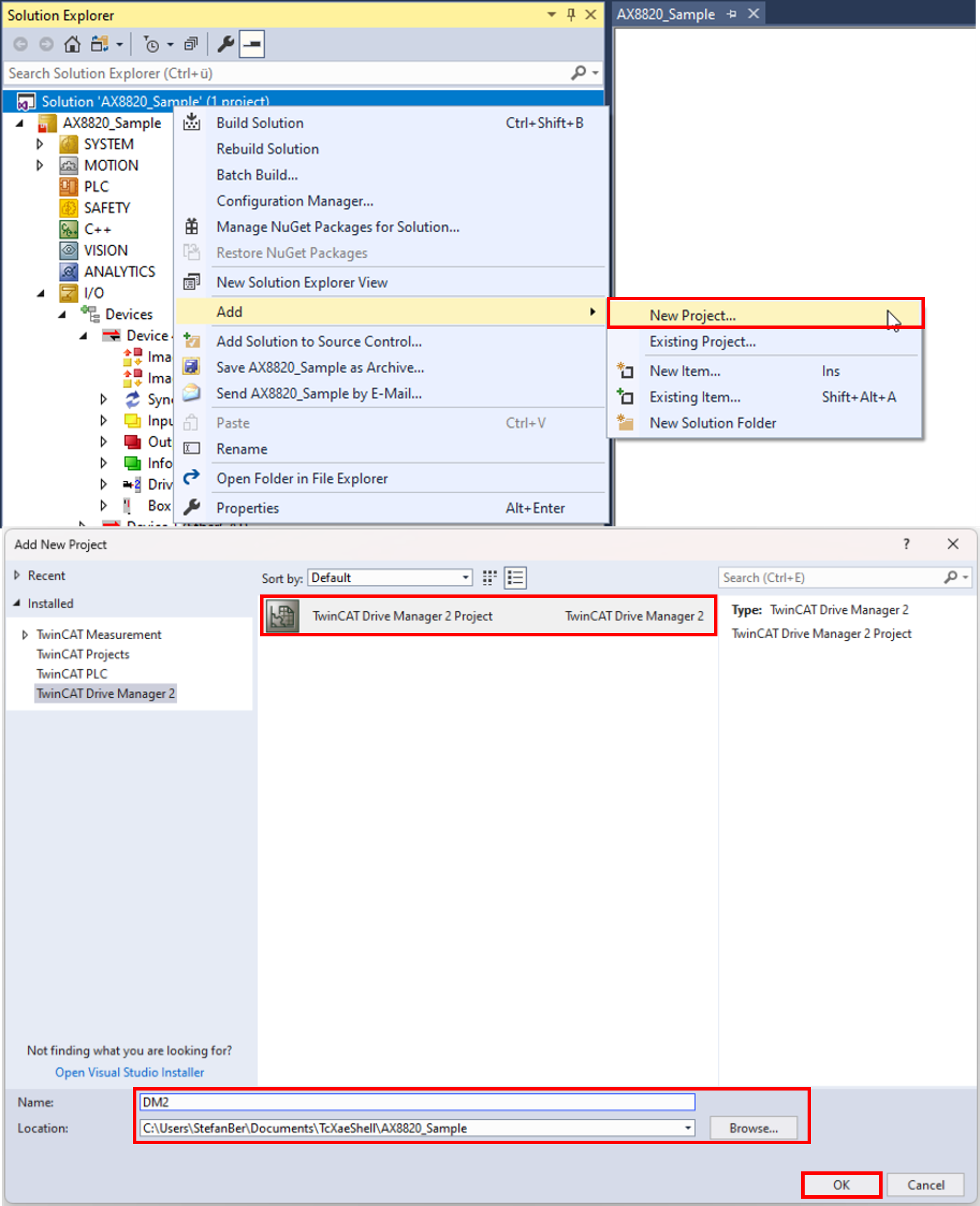
A TwinCAT Drive Manager 2 project is required for further configuration of the AX8820.
- ►Add a TwinCAT Drive Manager 2 project to the TwinCAT Solution
Quick initial configuration
ٔ
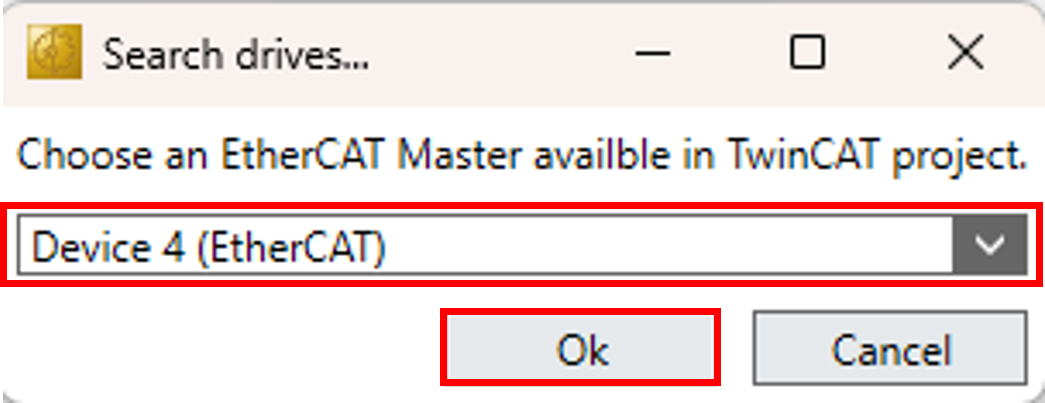
The Search drives... window opens automatically and starts a dialog for a quick initial configuration of the drive components.
- ►In the drop-down menu, select the EtherCAT master to which the AX8820 is connected
- ►Click Ok
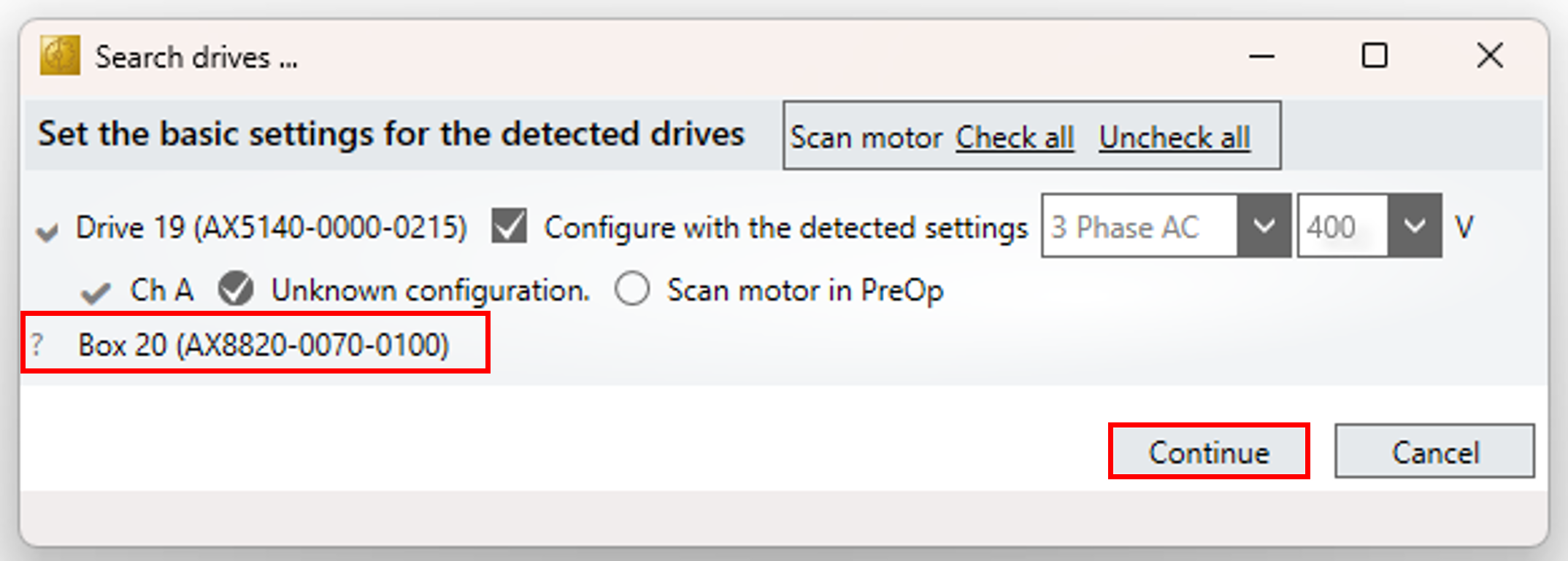
The drive components connected to the EtherCAT segment are listed.
- ►In the Search drives... dialog box, select the Scan motor in PreOP checkbox to automatically scan connected motors with an electronic nameplate.
- ►Confirm the Search drives... dialog box with the Continue button to execute the scan
![]() | Scan of the connected motors If servo drives are found, the electronic nameplate of the connected motors can be scanned. The read motor parameters are automatically transferred to the configuration. The scanned motors are displayed in green. |
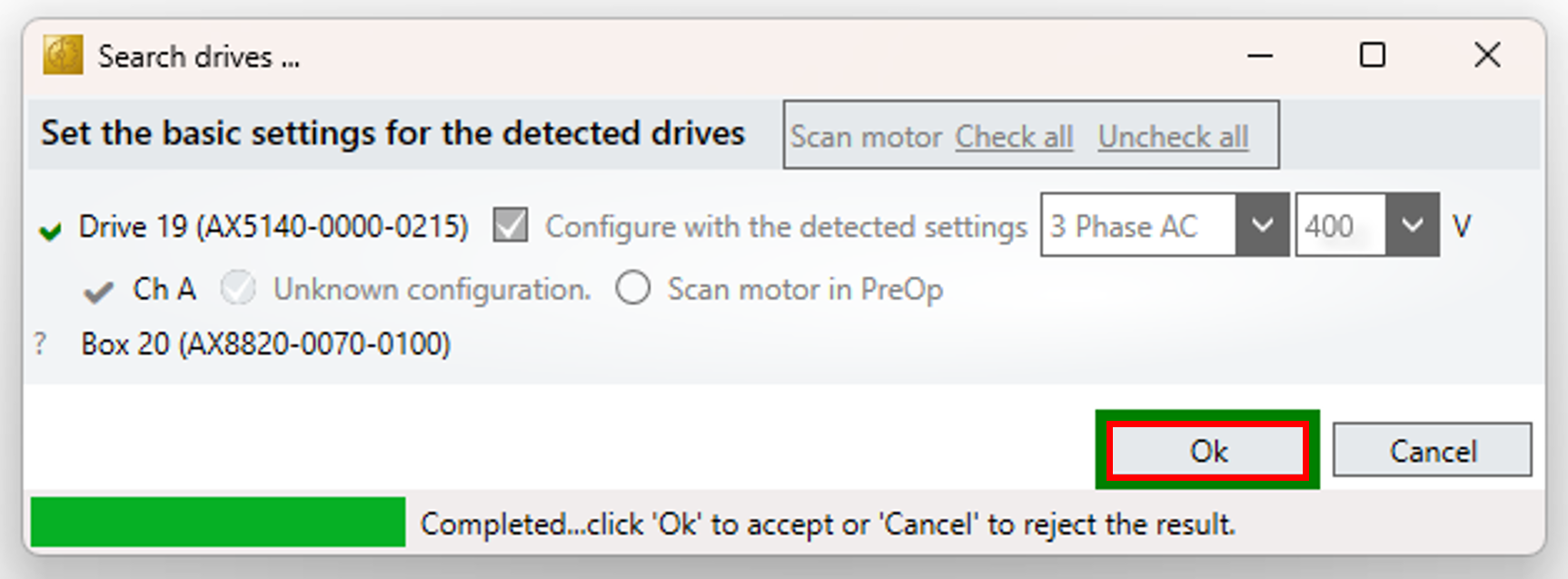
- ►In the Search drives... dialog box, confirm the transfer of the drive components found to the TwinCAT Drive Manager 2 project with Ok
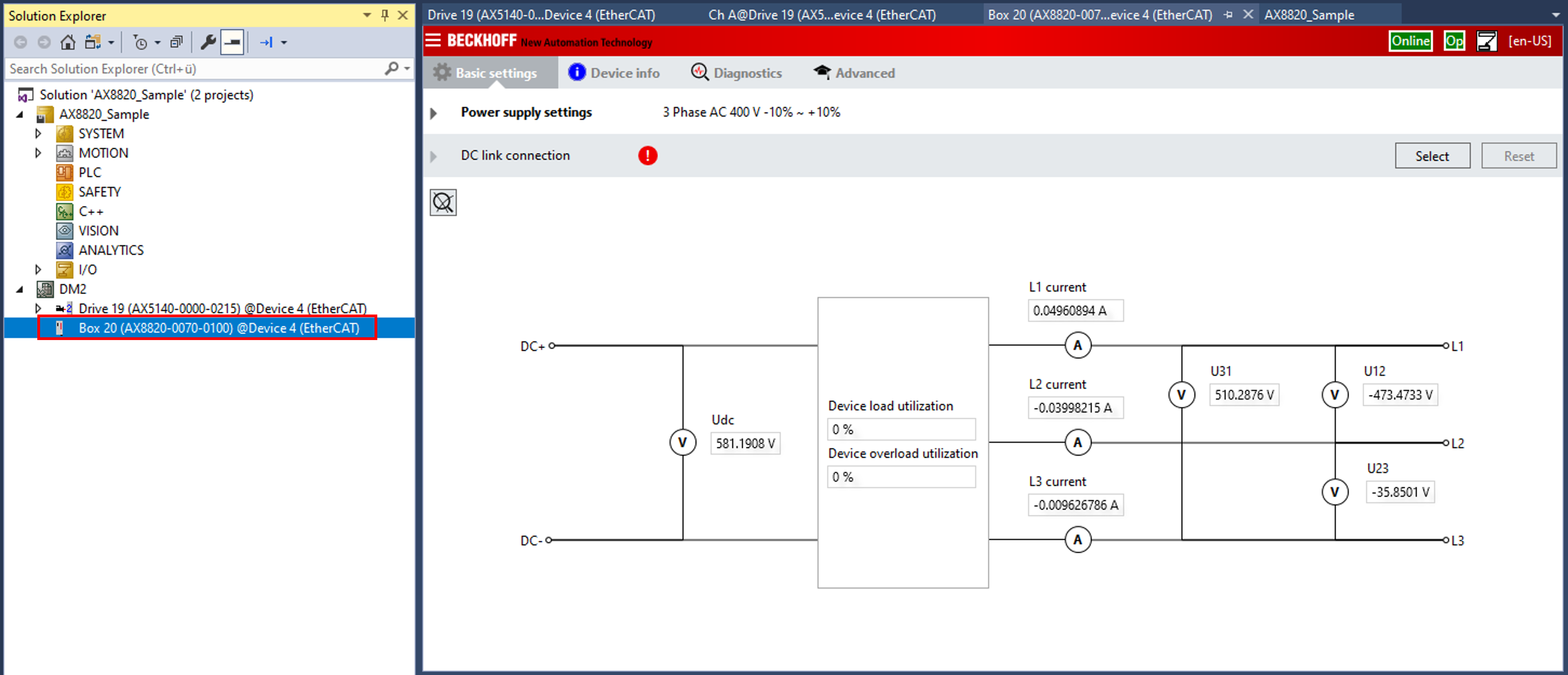
The view jumps back to the TwinCAT Solution.
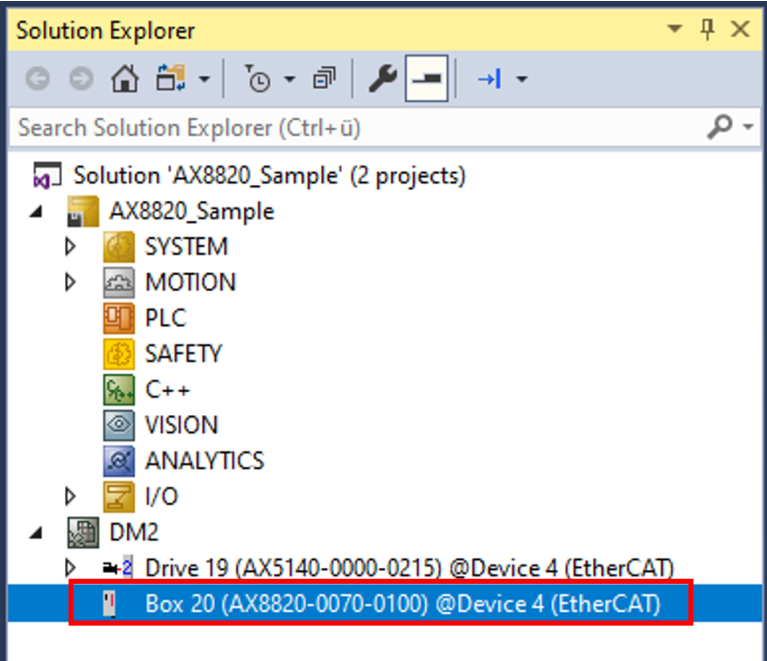
After the scan, all drive components found are listed under the TwinCAT Drive Manager 2 project node.
- ►Double-click on the AX8820 in the list to display the Basic settings tab
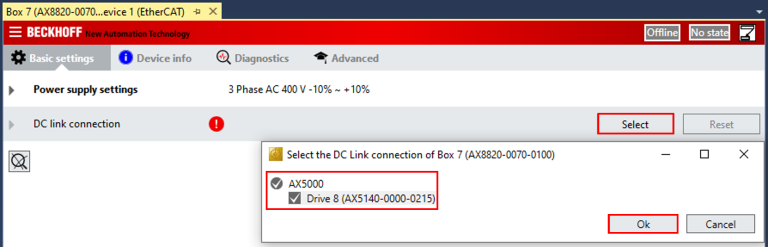
The standard view of the AX8820 universal regenerative unit is the Basic settings tab, which is used for further configuration.
- ►Click the Select button in the DC link connection section to specify the DC link connection
- ►In the Select the DC Link connection of Box ... dialog box, select the corresponding DC link connection to the connected servo drive
- ►Click Ok.
![]() | DC link connection to another system It is possible to select an DC link connection to an AX8000 system, provided the system is in the same EtherCAT network. However, only one connection to an AX5000 or AX8000 can be established. |
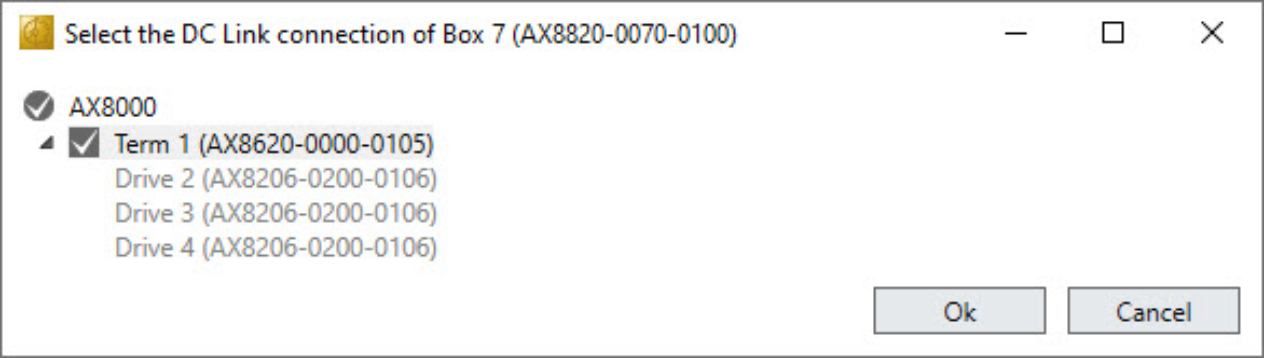
Graphical illustration
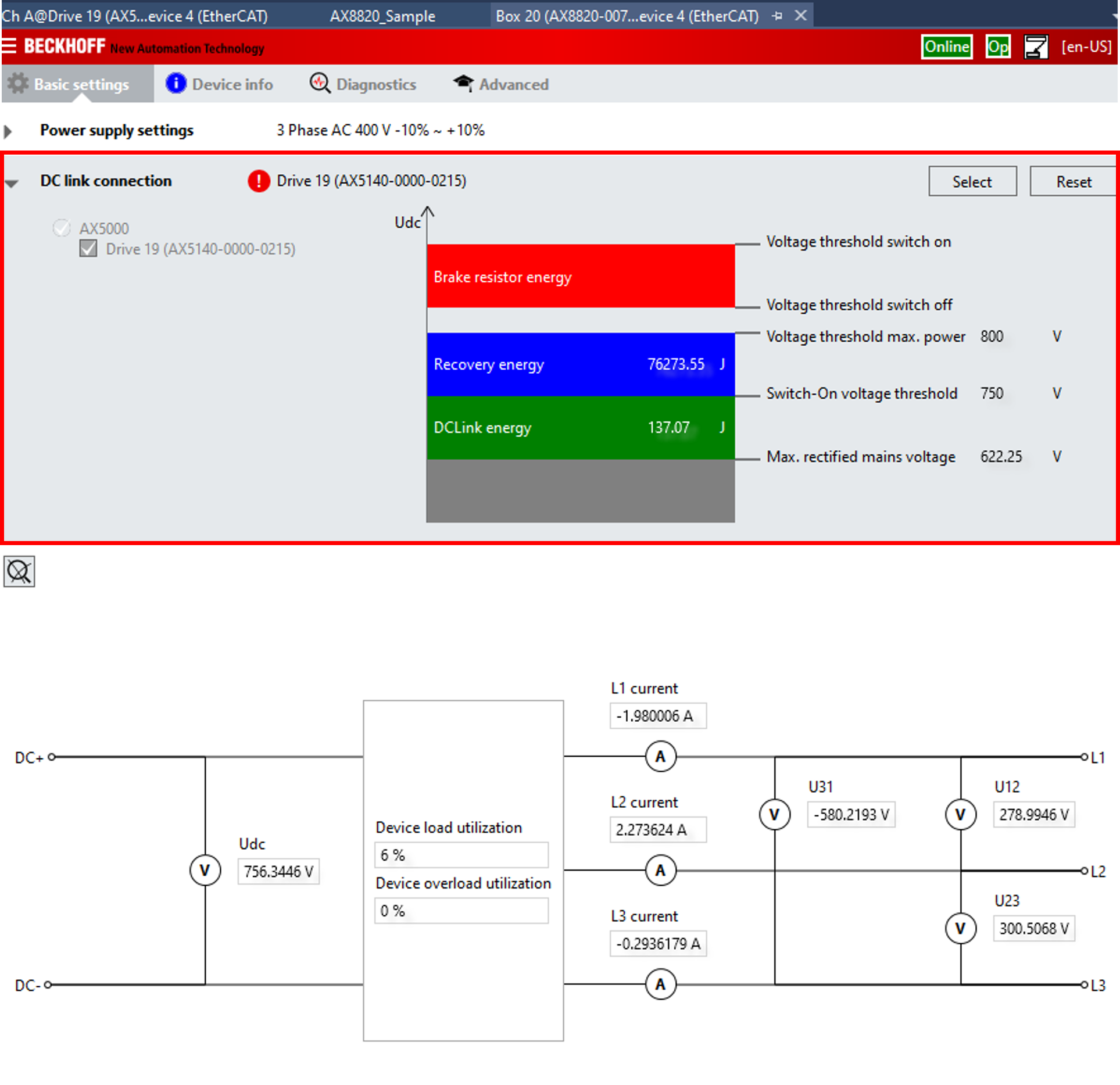
After selecting the Basic Settings, the DC link connection to the selected device and the energy management are displayed graphically in the section:
- The switch-on thresholds and switch-off thresholds are displayed
- The energy stored in the DC link is displayed in the DCLink energy area (green)
- If the AX8820 feeds energy back into the mains, the corresponding value is displayed in the Recovery energy area (blue)
Advanced Settings
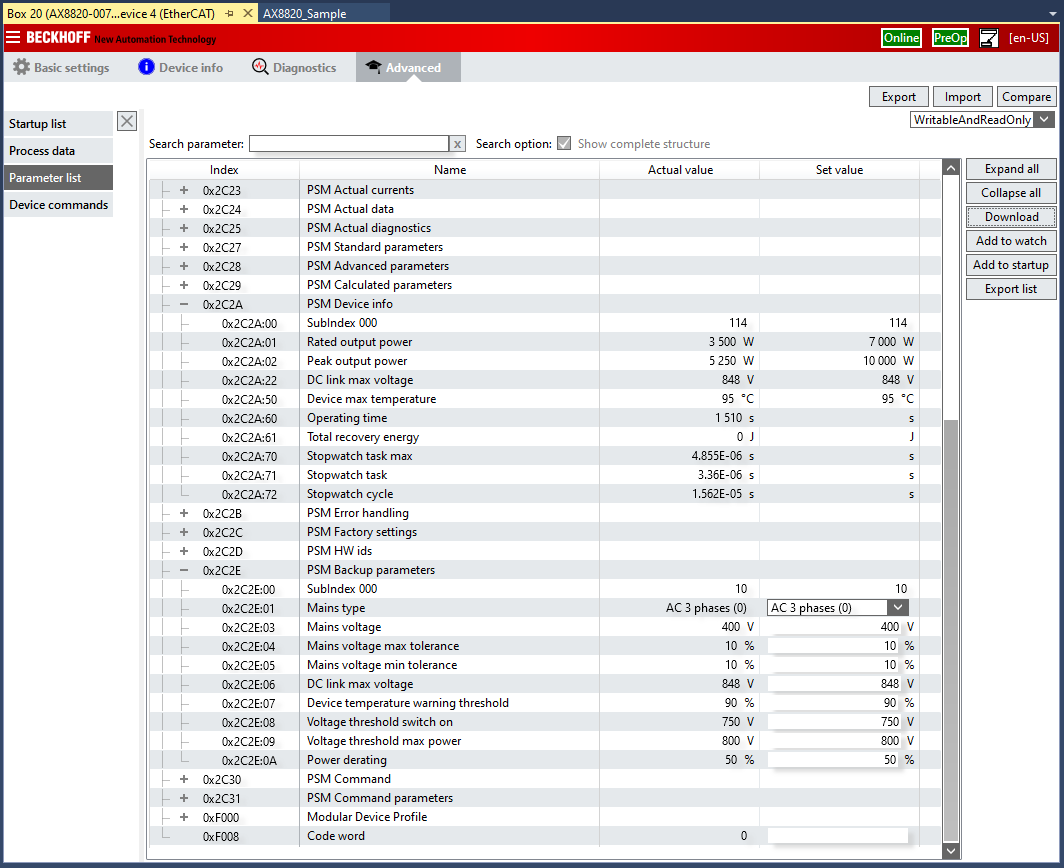
Further settings can be made in four sections in the Advanced tab.
The Parameter list section is used to set advanced parameters such as the switch-on thresholds, the power factor and the compensation mode.
- ►Setting the advanced parameters if necessary
Additional process data
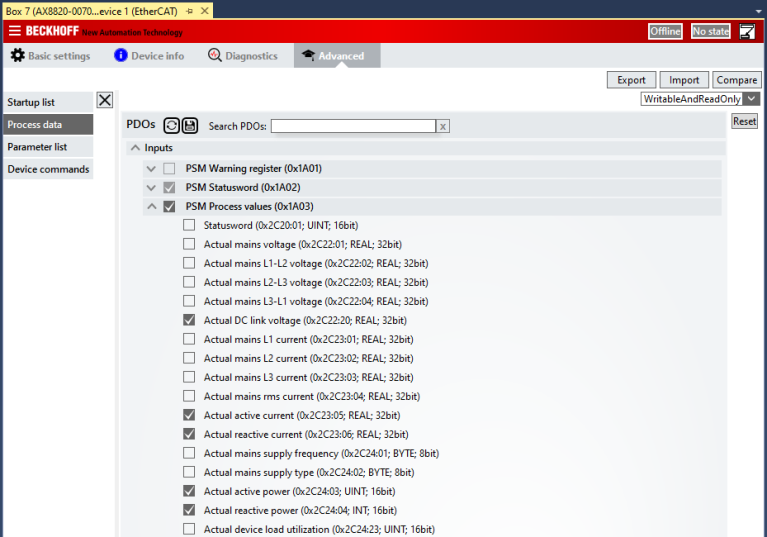
The current performance data of the AX8820 can be recorded for diagnostic purposes, e.g. with the TwinCAT Scope View, or analyzed in the PLC. The corresponding process data to be provided for this purpose is selected in the Process data section.
- ►Select the process data to be displayed via the checkbox
Activation of the configuration
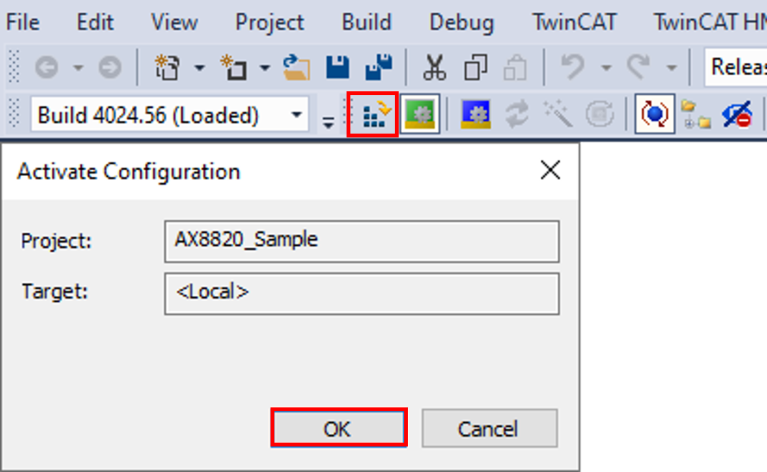
The selected settings take effect when the configuration is activated. The parameter settings are also saved in the EEPROM of the AX8820 by activating the configuration. The AX8820 is fully functional if the EtherCAT connection is interrupted.
- ►Activating the configuration