Operation without modulo
![]() | Application with gear unit and encoder In the following an encoder with 4096 revolutions and a gear unit with a ratio of 1:5 is shown. |
If the maximum encoder position at 4096 revolutions is exceeded, the encoder begins to count from zero again. The encoder position can no longer be used to detect that 4096 revolutions have already been made.
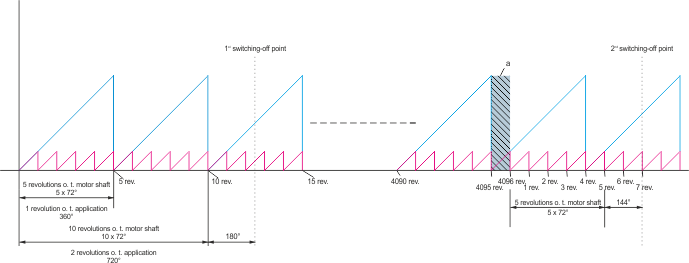
Switch-off point 1
The first switch-off point is at 12.5 motor revolutions or 2 application revolutions + 180°. The encoder provides the value correctly after the machine is switched on again.
Switch-off point 2
The second switch-off point is at 4103 motor revolutions or 820 application revolutions + 216°. Due to the overflow, the encoder has not taken the revolution in range [a] into account. It shows seven motor revolutions, but only one application revolution + 144°. One motor revolution is missing, which corresponds to 72° of the application.
Determine axis position
To determine the correct axis position, the overflows or the resulting position offset must be stored.