Configuration
Make sure that the scaling is set correctly by the application in relation to the first feedback system. Consider their mechanics and any speed increasing and reducing ratios that may be present.
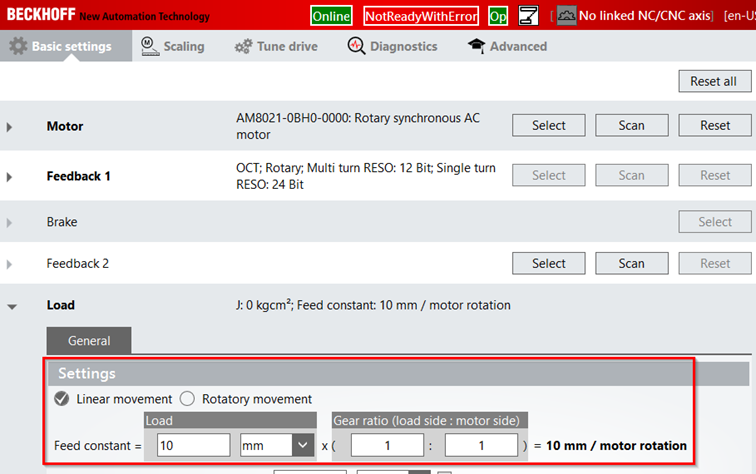
Clicking the Select button opens the window for selecting a second feedback.
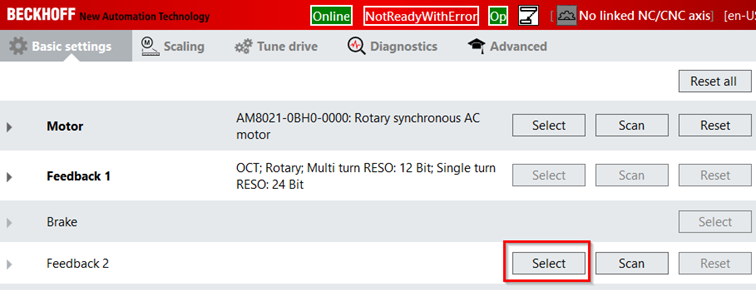
Select the feedback and confirm with OK.
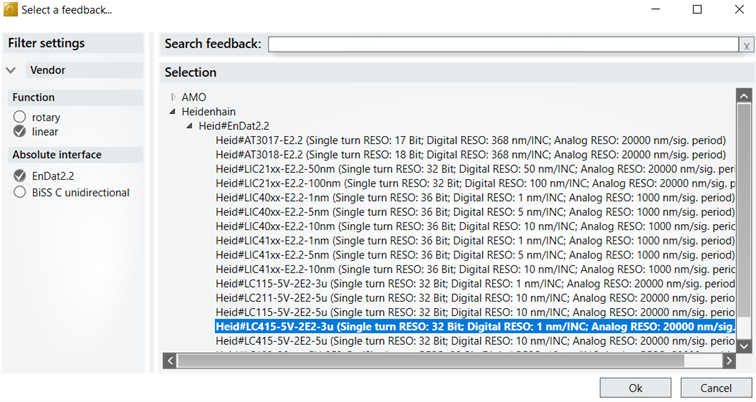
In the next step, a dialog box opens to specify the scaling of the second feedback system.
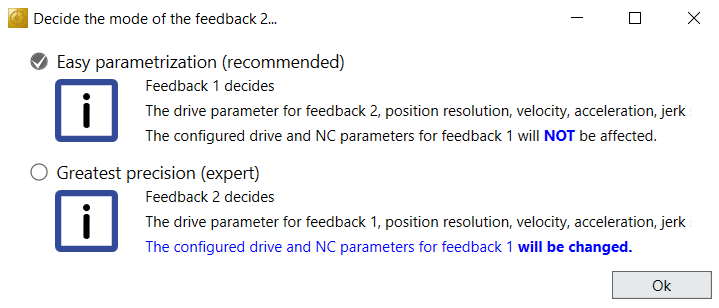
Easy parametization (recommended): the scaling of the second feedback is referred to the first feedback. Settings from the NC are not changed.
Greatest precision (expert): the scaling of the first feedback is referred to the second feedback. With this setting, the scaling in the NC axis must be adjusted. The necessary changes are made by DriveManager 2.
A summary of the changes in the AX8000 Startup list is displayed in the last dialog box.
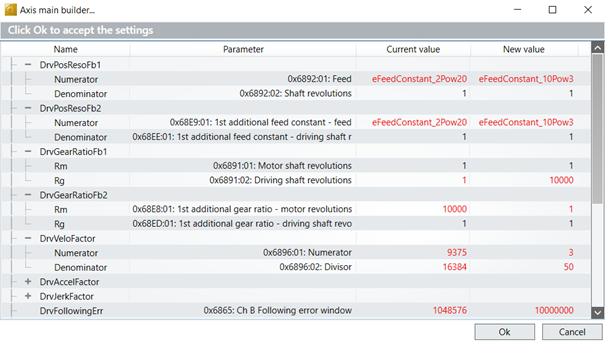
If the Greatest precision mode was selected during commissioning, the necessary changes in the NC must be applied by clicking on Save NC parameters.
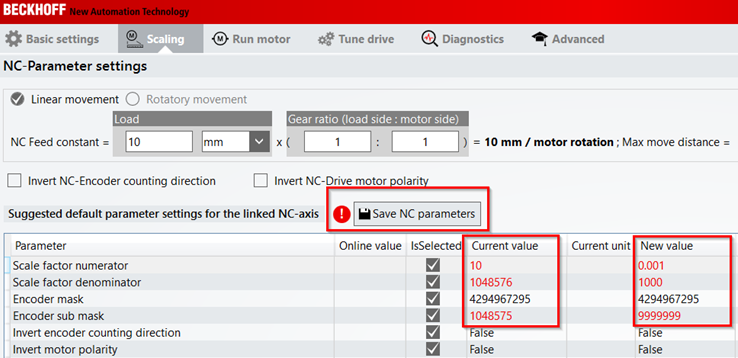
Activate the configuration and check whether the two feedback systems have the same counting direction.
- Make a note of the values.
- Ch A Position Actual Value(0x6064).
- 1st additional position actual value(0x60E4:01).
- Move the axis a little bit.
- Check the two values again and match the counting direction.
If the counting direction is opposite, then the counting direction can be adjusted by the second feedback in the range of Basic settings.
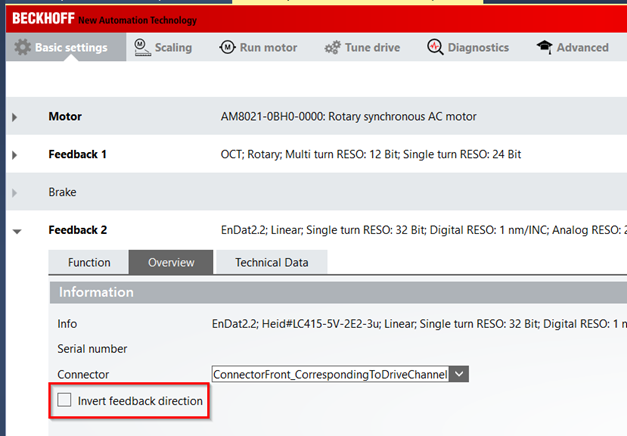
| |
Attention After the first activation of the configuration with a BiSS-C or Endat 2.2 feedback, the AX8000 requires a 24 V DC Power Cycle. The message Need cold start (0x5193) draws attention to this. |
The operation mode CSP (Cyclic synchronous position mode) can be switched to CSP2 (Cyclic synchronous position mode secondary feedback) if the counting direction of the feedback systems is identical.
With this change the DriveManager2 will insert the position value from the second feedback into the process image and link it to the NC.
After activating the configuration, the position is controlled to the second feedback.
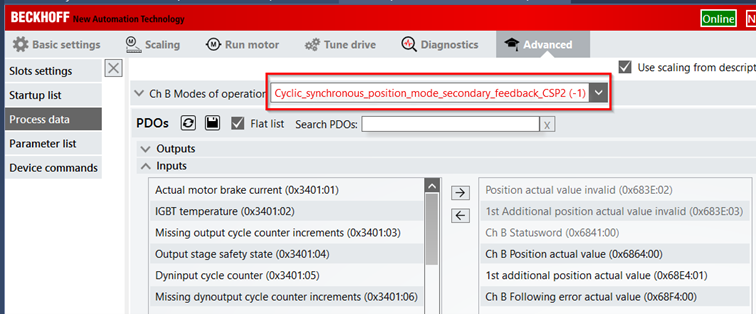