Firmware Update
The firmware of the AX5000 is a complex software, which is absolutely necessary for the operation of the servo drive. The servo drives are subject to a constant process of further development and improvement and, hence, the firmware is also under constant development, so that the latest technological innovations can also be used.
Dual Use (EU 1382/2014)
As published on December 30, 2014 by EU Commission Delegated Regulation 1382/2014, standard frequency inverters – and with that also Beckhoff products AX5000 – become newly classified Dual-Use items: the item list Annex I of the Dual-Use Council Regulation 428/2009 has been changed accordingly, Frequency inverters (listed in item position 3A225) with a „ rotation field frequency of 600 Hz or more“ are now export controlled items. As a consequence, some modifications have to be noticed.
Firmware versions without extension (Dual Use conform) can be used in consideration of Hardware Versions with following drives only:
- HW Version 1.0 (AX5xxx-0000-x0xx): Serial Number < 68.000
- HW Version 2.0 (AX5xxx-0000-x20x): Serial Number < 140.000
- HW Version 2.0 (AX5xxx-0000-x21x)
This Firmware versions with extension (Dual Use conform) can be used in consideration of Hardware Versions with all drives. These versions support both rotational field frequency bands (<600 Hz, >= 600 Hz) depending on product hardware. For products with option „x21x“, shipment as single part may be subject to export control regulations.
Example Firmware file name
Firmware file name of a HW2-Firmware version, which is "Dual Use conform": AX5yxx_xxxx_0203_v2_06_b0016_dual_use_conform.efw
Firmware file name of a HW2-Firmware version, which is NOT "Dual Use conform": AX5yxx_xxxx_0203_v2_06_b0012.efw
Dependency Motor speed - Rotation field frequency
n = f max x 60 / pp
nmax = max. Motor speedl
f = Rotation field frequency of the servo drive
pp = Amount of motor pole pairs
For f = 599 Hz the motor speed is:
Amount | Amount of | max. motor speed | AM8000 |
---|---|---|---|
2 | 1 | 35.940 | - |
4 | 2 | 17.970 | - |
6 | 3 | 11.980 | AM801x, AM811x, AM802x, AM812x |
8 | 4 | 8.985 | AM8x3x, AM8x4x, AM8x5x |
10 | 5 | 7.188 | AM8x6x, AM807x |
![]() | Check your application – Dual Use regulation Please compare the max. attainable motor speed (rpm) with the required speed (rpm) of your application. |
Firmware version on the AX5000
The current firmware version of the AX5000 is located in “IDN S-0-0030 - Manufacturer Version” and can be displayed using the TCDriveManager as follows: In the TwinCAT System Manager, mark the servo drive (1) whose firmware version you would like to know. Open the TCDriveManager (2) and click “Device Info” (3). A window opens and the current firmware version (4) appears in the “IDN S-0-0030”.
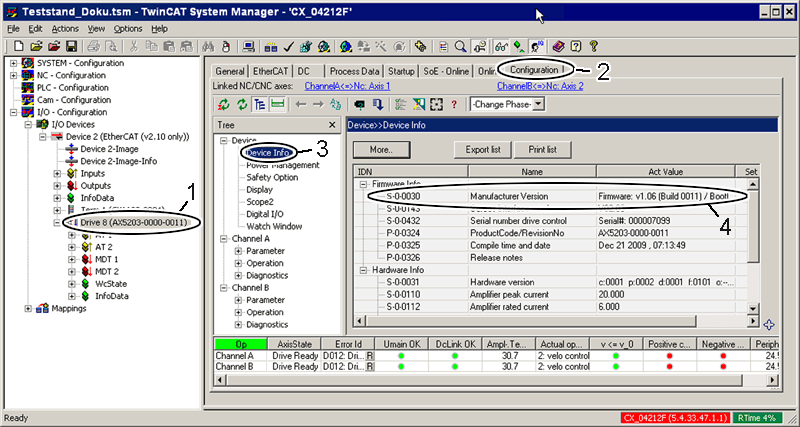
Update to a new firmware version
Read please the Release Notes carefully before the update. All important changes and additions to the individual firmware versions for the servo drives are in the corresponding file in the download area on our homepage.
![]() | Never touch a running system! This old IT concept applies more than ever today, in these times of the most complex systems with ever decreasing cycle times. Please do not perform firmware updates on a system that is working well without a reason, unless requested to do so by Beckhoff Automation. |
![]() | Update only within a version number! We recommend firmware updates only within the same version number (e.g.: V.1.05 (Build 0003) to V.1.05 (Build 0007). If you want to update from V.1.05 to V.1.06, for example, you will need to make further adjustments in TwinCAT. In accompaniment to that, we do not recommend performing a so-called “downgrade” to a lower version number. |
| |
Do not work on live equipment! The 24 V supply (plug “X03”) must be connected to the servo drive to be able to perform a firmware update. Make sure that the power supply (plug “X01”) is disconnected from the servo drive, so that uncontrolled movements of the equipment cannot occur. |
Update preparation
So that you can perform a firmware update, a connection must be made to the computer with TwinCAT that controls the AX5000. It is quite usual for you not to be in the area where the equipment is operated. That is not also necessary, because there are three different procedures for establishing a connection:
1.) Direct accesses to the control computer
You are in the same place where the equipment is operated and can work directly on the control computer. In this case you can continue immediately with the next chapter “Performing the update”.
2.) Remote access to the control computer
You are in a different place and have no direct access to the control computer. In this case you can also perform a firmware update on the control computer using one of the remote connections (VPN tunnel with remote desktop, VNC etc.) that are usual in the IT world. Please make sure that the firewall is configured accordingly for the remote connection and that you have the necessary rights. After establishing the remote connection, you can continue with the next chapter “Performing the update”.
3.) Remote access by ADS
You are in a different place and have no direct access to the control computer, or the control computer is in a cleanroom or the like. In this case you can also perform a firmware update via remote access by ADS. Please read in the Online Information-System how to implement remote access by ADS. Afterwards you can continue with the chapter “Performing the update”. The Online Information System is multilingual!
Selection of the Target system
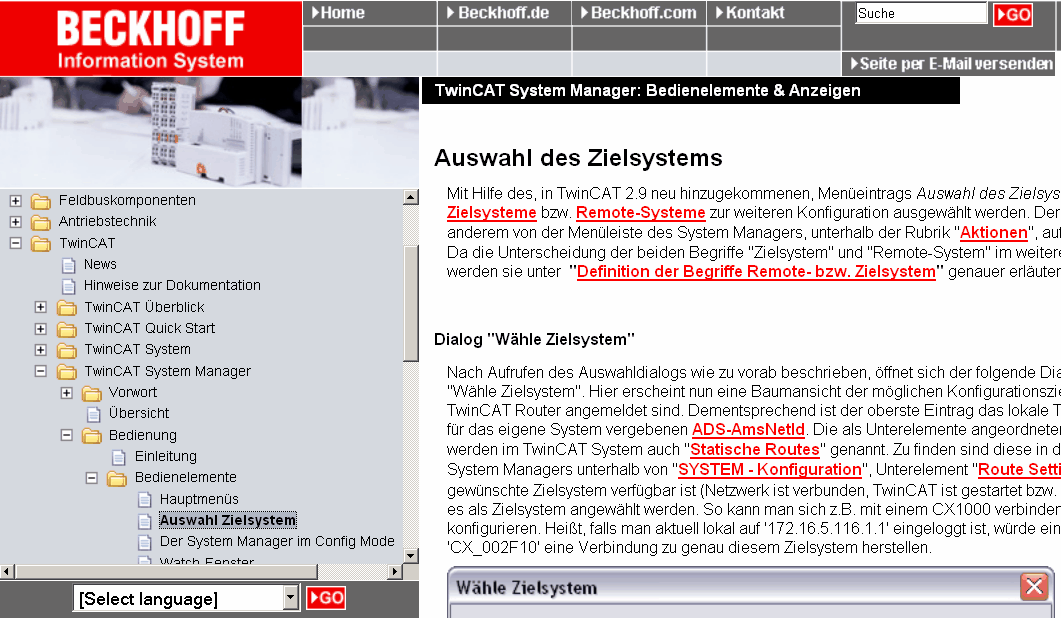
Performing the update
Click the button (1) in the TwinCAT System Manager to enter the configuration mode. Confirm the query with OK (2). After that a further window appears which must be confirmed with Yes (Ja) (3). Deactivate the “Free Run” with No (Nein) (4).
The system is now in “Configuration mode”.
|
|
|
To perform the firmware update, you must click the “Online” tab (6) in the “EtherCAT Device” (5). If you want to update several devices, you can select the respective servo drives (7) together; in the case of one device, select only the one servo drive. Subsequently, click with the right mouse button inside the selected area and select the command “Firmware Update” (8) in the command overview.
In the place where you have stored the desired firmware version, selected the firmware file (9) and click “Open” (10). Confirm the window that then opens with “OK”; the firmware update is then performed. After successful completion you must click OK (11) in the concluding “Function Succeeded” window.
|
|
|
Subsequently, TwinCAT must be brought from configuration mode back into operating mode. To do this, click the button (12) and confirm the query that appears with “OK” (13).
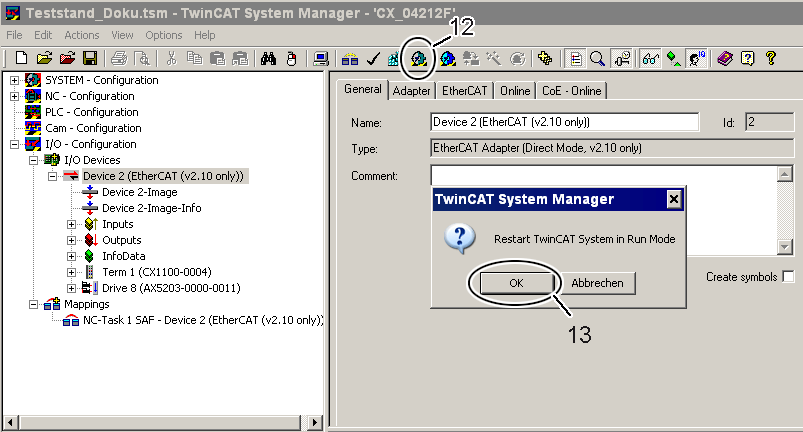
![]() | Update failed! If the firmware update is aborted with an error message, you should try again. If the abortion occurs several times, please start a further attempt with another copy of the firmware file. |