Special motor connections
Linear motors of the AL2xxx series
Connector box
With the Beckhoff AL2250 connector box you can simply connect the motor, encoder and thermal protection contact cables of the AL2000 linear motor range with the trailing cable motor and encoder cables of the AX5000, AX2500 and AX2000 range of servo drives
Appropriate use
The connector box is just for connection to the motor, encoder and thermal protection contact cables of the AL2000 linear motor range with the trailing cable motor and encoder cables of the AX5000, AX2500 and AX2000 range of servo drives.
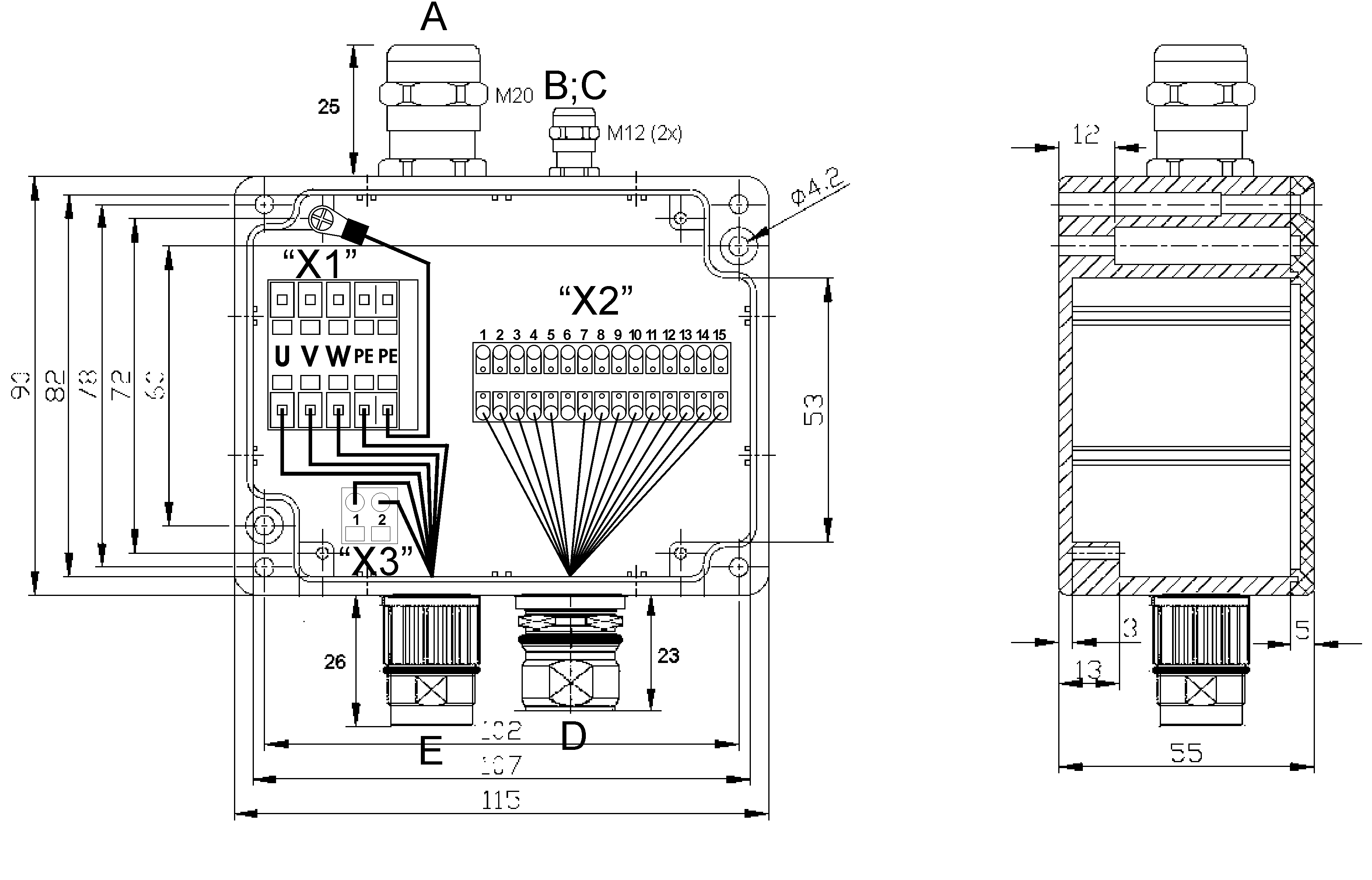
A: | Cable bushing and fuse for the linear motor cable. | E: | Connecting socket for the standard motor cable to the servo drive. |
B: | Cable bushing and fuse for the linear motor encoder cable. | X1: | Terminal strip for the linear motor connection cable. (The side for connection to “E” is already wired) |
C: | Cable bushing and fuse for the linear motor thermal protection contact cable. | X2: | Terminal strip for the encoder and thermal protection contact connection cable. (The side for connection to “D” is already wired) |
D: | Connecting socket for the standard feedback cable to the servo drive. | X3: | Thermal protection contact connection. Contacts “1” and “2” are bridged on the board with contacts “7” and “14” of “X2”. (The connection to “E” is already wired). |
| |
Risk of injury through electric shock! Remove the motor and feedback lines from the connector box to the servo drive when you open the connector-box. |
![]() | Attaching the connector box! The linear motor cables are not for trailing cables; hence the connector box has to be fixed on the moving part of the linear motor. |
Unscrew the cover and fix the connector box with 2 M4 screws on the carriage of the linear motor.
Motor cable:
Strip the wires of the motor cable and fit wire end sleeves.
Twist the screen of the motor cable and solder on a cable with a minimum diameter of 1.5 mm2. Fit wire end sleeves or a cable lug to the free end. Place the nut of socket “A” over the motor cable and feed the wires through the socket “A” in the box and screw the nut onto socket “A”. Fit the shielded and PE cables with a “PE” connection and the power wires on connection “X1”.
Encoder cable:
Strip the wires of the encoder cable and fit wire end sleeves.
Twist the screen of the encoder cable and solder on a cable with a minimum diameter of 0.75 mm2. Fit wire end sleeves or a cable lug to the free end. Place the nut of socket “B” over the encoder cable and feed the wires through the socket “B” in the box and screw the nut onto socket “B”. Fit a “PE” connection to the shielded cable. Wire the signal wires to the “X2” connection as per the table.
Connection pin | Signal description | MES | LIKA | SIKO | NJ* |
---|---|---|---|---|---|
X1-PE | PE / GND | shield | shield | shield | wh / gn |
X2-1 | COS - | red | orange | green | red |
X2-2 | GND | white | black | black | white |
X2-3 | SIN - | yellow | blue | orange | yellow |
X2-4 | + 5V DC | brown | red | brown | brown |
X2-5 | DATA + / Z + | --- | white | blue | grey |
X2-6 | n.c. | --- | --- | --- | --- |
X2-7 | PTC | --- | --- | --- | --- |
X2-8 | Clock+ | --- | --- | --- | --- |
X2-9 | COS + | blue | green | yellow | blue |
X2-10 | GND sense | grey | --- | --- | --- |
X2-11 | SIN + | green | yellow | red | green |
X2-12 | + 5V sense | pink | --- | --- | --- |
X2-13 | DATA - / Z - | --- | --- | violet | pink |
X2-14 | PTC | --- | --- | --- | --- |
X2-15 | Clock- | --- | --- | --- | --- |
Thermal protection contacts cable
Strip both wires of the thermal protection contact cable and fit wire end sleeves.
Twist the screen of the thermal protection contact cable and solder on a cable with a minimum diameter of 0.75 mm2. Fit wire end sleeves or a cable lug to the free end. Place the nut of socket “C” over the thermal protection contact cable and feed the wires through the socket “C” in the box and screw the nut onto socket “C”. Fit a “PE” connection to the shielded cable. Fit both thermal protections contact wires to contacts “7” and “14” of connection “X2”.
Retighten the connector box cover.
SEW motors from the “DFS / CFM” range with stopping brake
The stopping brake of the SEW motors must be connected via a brake rectifier, to guarantee the “quick activation of the brake”. A 3-wire connection cable is required for this. The following schematic diagram shows the correct connections of the motors to the AX5000.
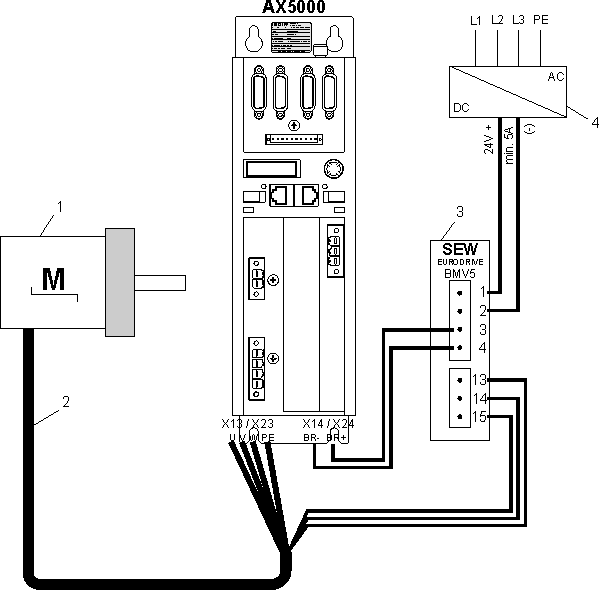
1 = SEW servo motor of the DFS/ CFM range
2 = Motor brake cable ZK4500-4xxx
3 = SEW- BMV5 brake rectifier
4 = Power supply unit with 5A minimum output current