Drive functions
| |
Hazard to individuals and devices! Please read the following functional descriptions carefully and parameterize the relevant functions. |
Stopping the drive
Quick stop (S-0-0372) and emergency stop (S-0-0429)
The two stopping procedures are defined using ramp functions which the AX5000 uses to stop the connected motors. The two ramp functions are parameterized using IDN S-0-372 (quick stop) and IDN S-0-0429 (emergency stop). The braking energy balance for the whole system must be borne in mind when parameterizing these IDNs. The max. deceleration is influenced by both mechanical and electrical limit values. The electrical limit results primarily from the available power. When this has reached the maximum, no further braking energy can be supplied, and the delay time will take correspondingly longer. A further electrical limit is the absorption of regenerative energy which is produced during braking. This energy is first absorbed by a DC link and, when this is saturated, internal, or external brake resistors take over the absorption of braking energy.
It is not necessary to activate these braking functions manually during normal operation as "normal" braking procedures are carried out by the set value generator. It is essential to manually actuate the braking functions during commissioning to assess the braking procedures.
Under certain circumstances "Quick stop" can be actuated using the bit "14" (enable drive) of IDN S-0-0134 (Master control word).
The "Emergency stop" is only actuated by a drive error and can be actuated using the parameter P-0-0310 (Error reaction verification) "Force error reaction: Closed loop ramp".
| |
Danger to persons from unexpected movements. After parameterizing the IDNs "S-0-0372" and "S-0-0429" for stopping the drive, the corresponding ramp function must always be tested manually again. This is necessary to ensure that the mechanical or electrical conditions enable reliable operation. |
Limit switch monitoring
A translatory drive motion generally results in a finite travel path. In order to be able to protect the mechanical end positions, limit switches must be installed at a distance s to the end positions. If one of the switches is actuated, then the servo drive stops the axis by means of a stop ramp (S-0-0372 or S-0-429).
Limit switch properties (P-0-0401) | |||
---|---|---|---|
Configuration | Reaction | Source | |
0 | No limit switch (default) |
|
|
1 | N/C contact | 0 = Axis generates an error and is stopped by the emergency stop S-0-0429. | |
2 | N/O contact |
This structure is available twice under IDN P-0-0401, i.e. for the negative and the positive limit switch.
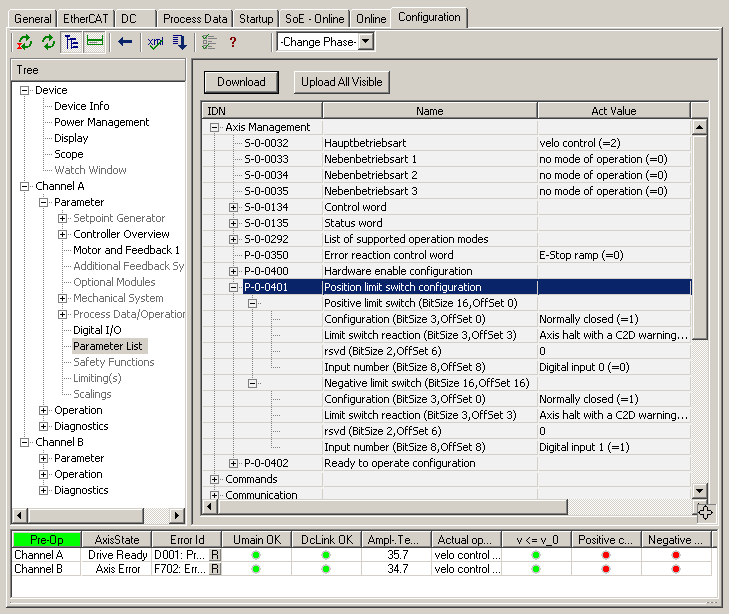
Example
A short example for calculating the distance between the limit switch and the mechanical limit stop is shown below:
Example | |||
---|---|---|---|
Parameter no. | Designation | Value | Unit |
S-0-0372 | Emergency ramp | 6283.18 | rad/s2 |
S-0-0429 | Stop ramp | 6283.18 | rad/s2 |
S-0-0091 | Maximum speed, bipolar | 6000 | rpm |
S-0-0079 | Rotational position resolution | 1048576 | inc/rev |
Machine data | Feed | 20 | mm/rev |
Distance between mechanical limit stop and switch:
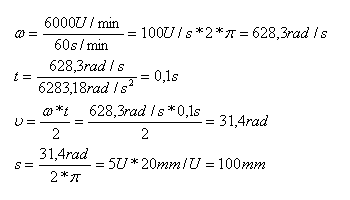
Hardware enable
On the AX5000 a hardware enable can be configured. This function operates in addition to the software enable originating from the controller via the bus system and a logical AND link. The digital input for the servocontroller is activated and allocated via parameter P-0-0400.
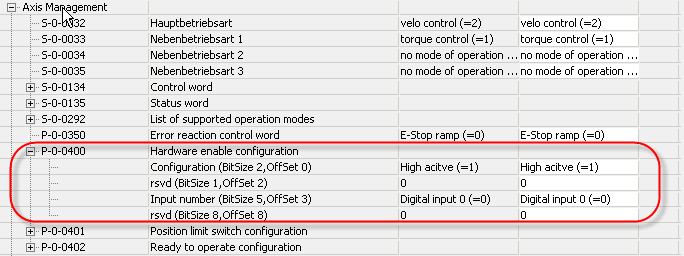
This function is not limited to a special input.
Ready to operate
The AX5000 can be integrated in the ready-chain of the machine via the device configuration. This function requires a digital input and a digital output. Activation of this function and allocation to the respective input and output is realized in parameter P-0.04002. Since only digital input no. 8 can optionally be configured as output, only digital output no. 8 is offered as output number.

(Electrical properties in preparation)
Controlling the motor brake
If the motor is equipped with a motor brake, this brake is controlled via the servo controller. The brake is configured via parameter P-0-0060. This parameter is part of the XML description of the motor. The brake can be locked and unlocked via the TcDriveManager as required.
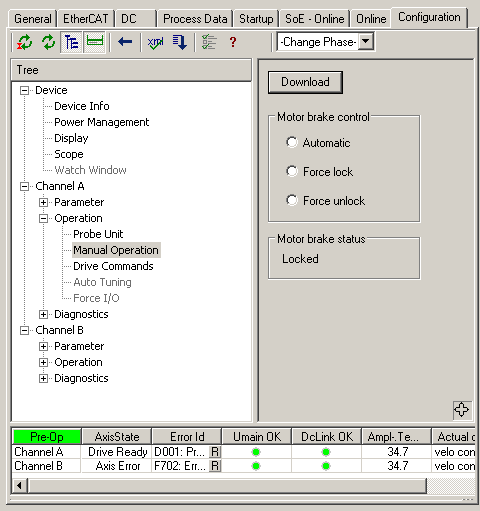
If the brake must be controlled from the application, parameter P-0-0096 is available as motor control word and P-0-0097 as motor status word. The following table shows the command sequence for unlocking and locking the brake from the PLC.
Unlock the brake | Lock the brake | ||
---|---|---|---|
Control word | Status word | Control word | Status word |
| 0x0000 |
| 0x0000 |
0x0002 |
| 0x0001 |
|
| 0x0002 |
| 0x0001 |
The brake response times are configured in parameter S-0-0206 for (enable) and parameters S-0-0207 (disable).
Mains voltage monitoring
The servo drive monitors the minimum and maximum values of the connected mains voltage. To this end the value of the connected voltage and the permitted tolerance values are specified. The diagram below shows the TCDriveManager configuration option. The section outlined in red is used for configuring the mains voltage with min./max. values. Mains phase monitoring is activated or deactivated in the section outlined in purple. Phase monitoring is always based on 3-phase mains.
![]() | Phase monitoring With a single-phase mains supply phase monitoring must be deactivated for the servo drive to work. |
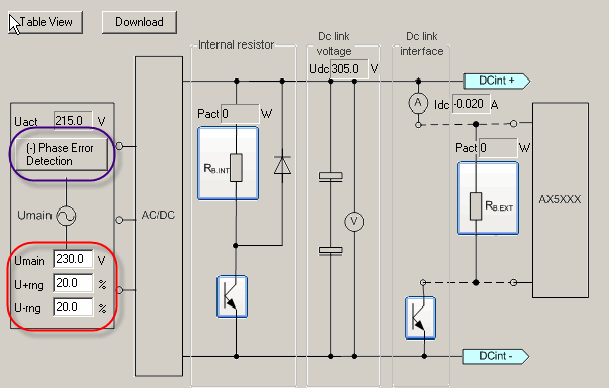
The values are limited to 50% in maximum and minimum direction. The relevant parameters are P-0-0201, P-0-0202, P-0-0203, and P-0-0204.
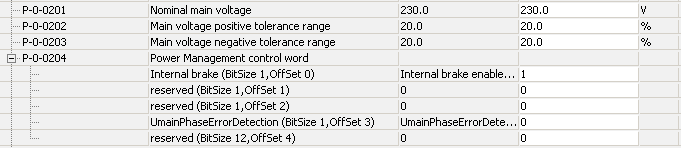
Active DC link integration
(in preparation)
Digital inputs and outputs
All AX5000 devices have 8 digital inputs, irrespective of the type (1- or 2-channel) (inputs 0 to 7). Input no. 7 can be reconfigured as output. The digital I/Os can be allocated to channel A or B.
The status of the digital inputs is represented in parameter P-0-0801. This parameter can be transferred in the cyclical interface, so that the information is available in the PLC and NC.
The decision to use input no. 7 as output can be implemented in two different ways, through allocation to the PLC output (P-0-0800), or through allocation of this bit to a drive function that sets this output as a result. An example for the second option is the ready to operate function of the servocontroller. If the PLC output is used the value is transferred via parameter P-0-0802.
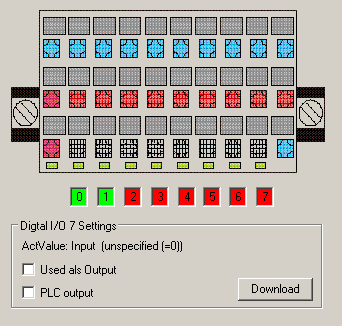
The differentiation between the controller and the PLC as the signal source is specified in parameter P-0-0801.
(Electrical properties in preparation)
Measuring probe functions
The measuring probe function enables the actual controller position to be stored event-dependent. This could also be achieved via the control unit, although with a velocity greater than 0 an error would be introduced that is proportional to the velocity. For this reason, this function is allocated to the drive, where the actual position is stored and transferred to the control unit almost without time offset, depending on the digital input or a combination of event signals.