Operating modes
In drive technology a distinction is made between the following operating modes:
- Current / torque control
- Speed control
- Position control
Electrical drives tend to be speed- or position-controlled. In the SoE standard the individual operating modes are specified via the standard parameter S-0-0032 (main operating mode).
S-0-0032 (main operating mode) | ||
---|---|---|
Bits 0-8 | Operation mode | Bit 3 |
0 0000 0000 | no mode selected |
|
0 0000 0001 | torque control |
|
0 0000 0010 | Velocity regulation |
|
0 0000 X011 | Position control with position encoder 1 (motor resolver MG) | 0 with following error / 1 without following error |
0 0000 X100 | Position control with position encoder 2 (external encoder EG) | 0 with following error / 1 without following error |
0 0000 X101 | Position control with position encoder 1 + 2 | 0 with following error / 1 without following error |
The diagram shows a typical control structure with higher-level position controller and subordinate speed and current controller.
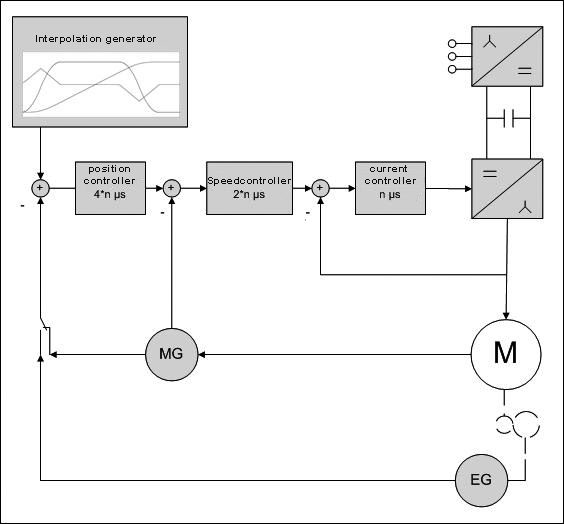
A cascaded controller structure consisting of current, speed and position controllers has proven to be necessary for achieving high dynamics and positioning accuracy. The diagram illustrates the time constants of the individual control loops, rising from inside to outside. Two operating modes are suitable for positioning: velocity set value specification or position set value specification.
Position specification
Fig. 1 also shows the interpolation generator. This can take the form of an external software or hardware solution or an option inherent in the servo drive. For the AX5000 TwinCAT PTP/NCI or TwinCAT CNC is used. This set value generator splits the travel command into small position segments. These segments have a temporal resolution that is set via the interpolation cycle (task time of the SAF task of the NC).
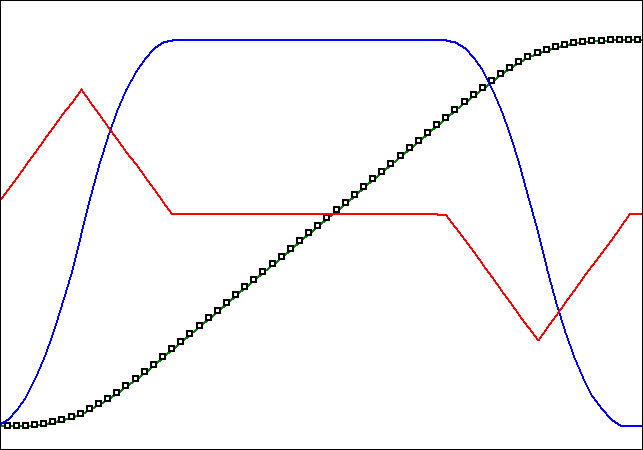
This mode is configured via parameter S-0-0032. The individual modes are shown in Table 1. In addition to the internal position controller velocity pre-control can be activated. If no pre-control is used the set value for the speed controller only consists of the product of the control deviation and the position controller gain.
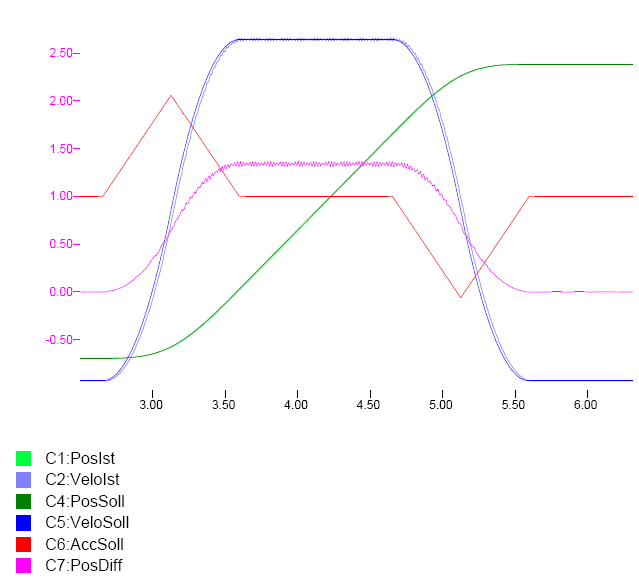
S-0-0032 (main operating mode) | ||
---|---|---|
0 0000 0011 | 0x03 | Position control with position encoder 1 (motor resolver MG) / with following error |
0 0000 0100 | 0x04 | Position control with position encoder 2 (external sensor EG) / with following error |
Pre-control is generally advisable. Depending on the application the weighting of this parameter can be set between 0 and 100%. The following block diagram shows two options. One option is to calculate the pre-control in the drive. Using a simplified technique, the set position at time n Sn is subtracted from the set position from the pre-cycle and divided by the cycle time. Another option is to use the set velocity of the interpolation generator.
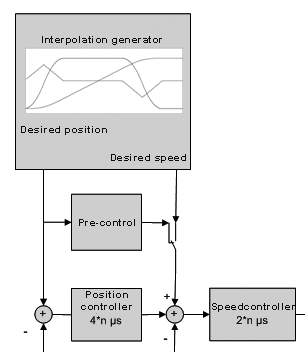
If velocity pre-control is used for positioning, the following error during the whole positioning process is relatively small (see Fig. 5).
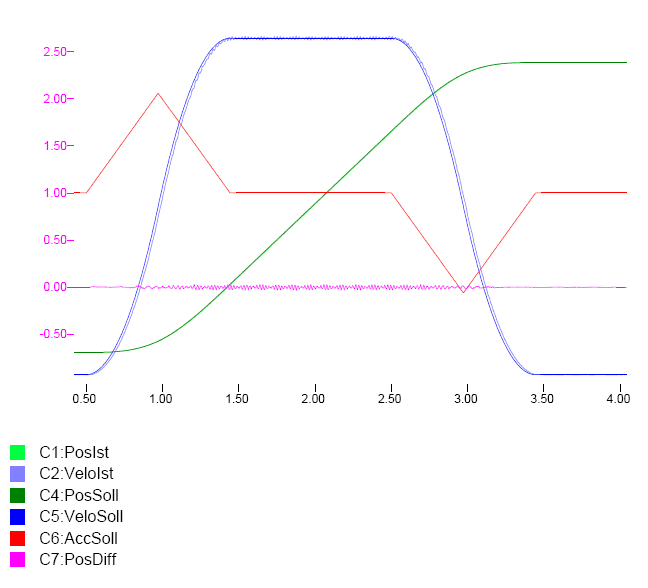
S-0-0032 (main operating mode) | ||
---|---|---|
0 0000 1011 | 0x0B | Position control with position encoder 1 (motor encoder MG) / without following error |
0 0000 1100 | 0x0C | Position control with position encoder 2 (external encoder EG) / without following error |
Velocity specification
If the servo drive has no position controller or if the set velocity has to be influenced with additional components, the position controller can be moved to the interpolation generator. In this mode is the travel command is not only split into small position segments but also into velocity segments. The set velocity calculated by the interpolator is complemented by the value calculated by the TwinCAT-PTP position controller due to a following error.
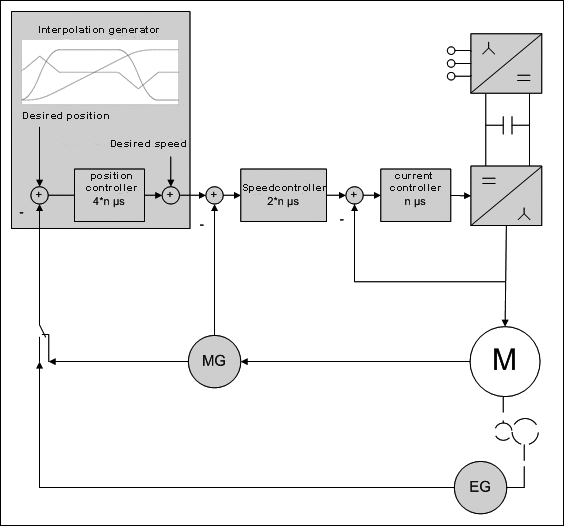
As for position specification, the interpolation points for the velocity set values have a temporal resolution that is greater than the interpolation cycle (task time of the SAF task of the NC).
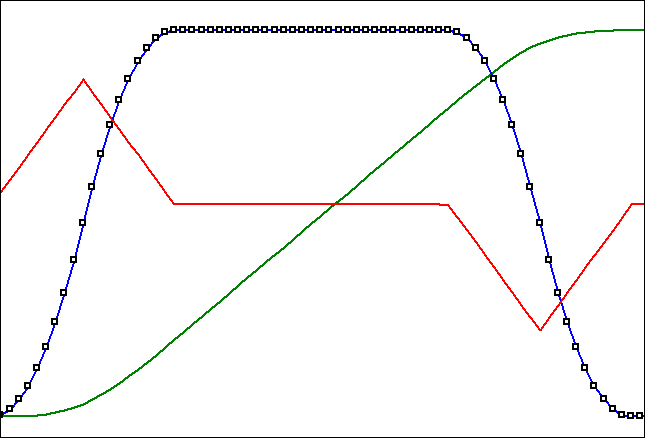
This mode is configured via parameter S-0-0032.
S-0-0032 (main operating mode) | ||
---|---|---|
0 0000 0010 | 0x02 | Velocity regulation |
A further mode is torque control. In this mode is the set torque is specified. The actual torque is returned as feedback. Torque control is handled by the drive. If the actual value is based on an external measuring point, regulation (set value generation) should be provided in the control system.
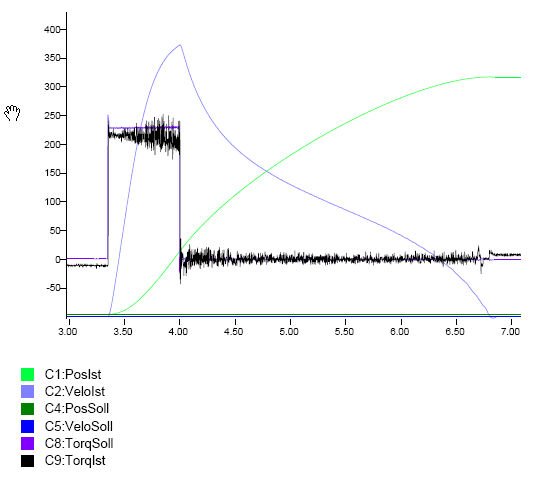
S-0-0032 (main operating mode) | ||
---|---|---|
0 0000 0001 | 0x01 | torque control |