Application example (emergency stop – stop category 1)
Components involved:
- Emergency stop device (control switch S1) according to ISO 13850 and control switch S2
- 1 safety input terminal (KL1904) and 1 input terminal (KL 1404)
- 1 safety logic terminal (KL6904) with function block "ESTOP"
- AX5801 Safety Card and servo drive from the AX5000 range
- Programmable logic controller (PLC) and EtherCAT fieldbus
By activating the emergency stop device (S1) inputs EStopIn1 and EStopIn2 of FB "ESTOP" are switched to state "0", resulting in outputs EStopOut and EStopDelOut of FB "ESTOP" being switched to state "0". As a result, a quick stop command is issued to the PLC and therefore the AX5000 via EtherCAT. The output EStopDelOut of FB "ESTOP" ensures that after a specified delay time the 24 V supply of the AX5801 Safety Card is interrupted. This causes the relays (REL1 and REL2) to release and both channels (motors) to be made torque-free via the internal deactivation procedure of the AX5000.
In the event of a fault the controlled shutdown (quick stop) may fail. The Safety Card becomes active once the delay time has elapsed, and all motors connected to the device run out. The risk analysis for the machine must indicate that this behavior can be tolerated. An interlock may be required.
The delay time must be set slightly longer than the maximum braking time of the quick stop.
Sticking relay contacts on the Safety Card are detected via input EDM1 of FB "ESTOP", and restarting is prevented.
When the emergency stop device is released again, the control switch (S2) must be operated (first rising then falling edge at the restart input of FB "ESTOP") in order to restart the AX5000.
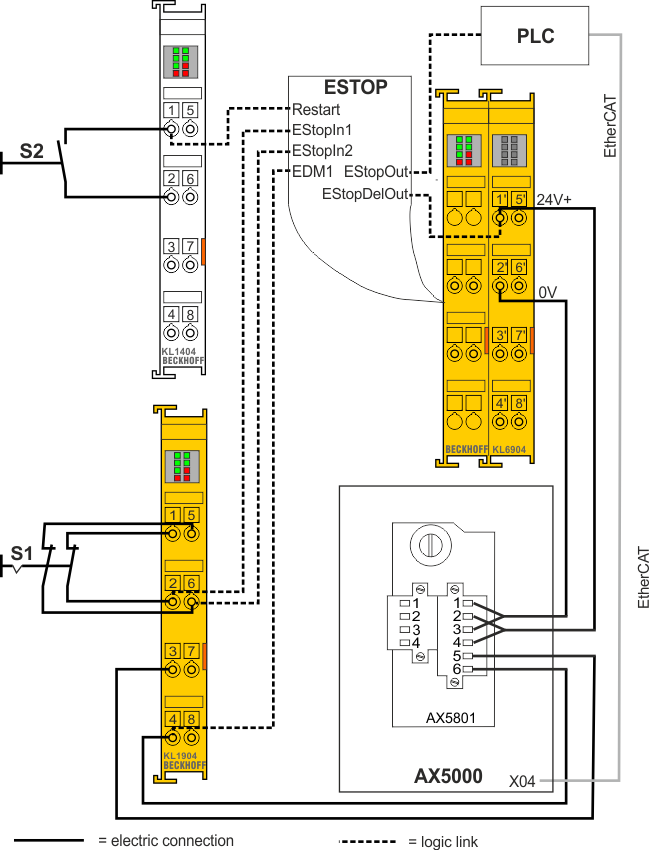