Parameterization in the System Manager
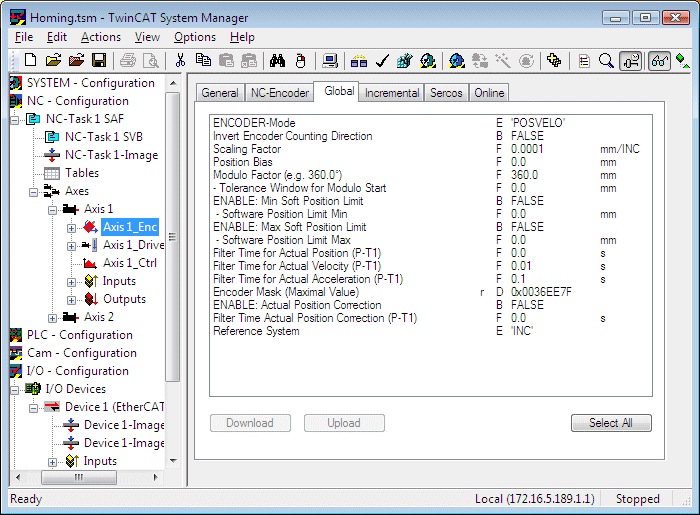
Reference System : The encoder parameters Reference System determines whether the encoder system used is incremental or absolute. In an absolute encoder system the encoder value is taken from the control system without modification.
Not all NC encoders support this optional parameter, i.e. only those types that offer a choice between absolute and incremental encoder reference system (measurement system) support it (e.g. SERCOS, KL5001, M3000, ProfiDrive, Universal). This choice determines whether the actual encoder position is interpreted and evaluated as an absolute or incremental position, based on an absolute or incremental reference system (measurement system).
In an absolute reference system no further processing takes place with regard to encoder counter value overflow or underflow. It is assumed that the counter value is unique within the axis traversing range and no encoder counter value overflow or underflow occurs. Otherwise there would be a discontinuity in the actual position, resulting in a position following error. Axis referencing via MC_Home is not possible. Instead, the actual position is calibrated once via the parameter Position Bias (zero offset / position offset).
In an incremental reference system axis referencing via MC-Home is generally required. In addition the NC automatically detects and accounts for encoder counter value overflow or underflow events, so that continuous axis operation is possible over many months ("infinite range").
Encoder Mask (maximamum value): The encoder mask determines the bit width for the incremental encoder position. The encoder mask is used for detecting and counting in range overflow events.
Scaling Factor: The scaling factor is multiplied by the incremental encoder position, including all overflows. From this an absolute axis position can be calculated with the parameterized physical unit.
Position Bias (zero offset): Position offset; moves the axis coordinate system relative to the encoder coordinate system. This value is mainly used in absolute encoder systems. In relative systems an offset is usually not required, since the system moves to a parameterized reference position after homing.
Invert Encoder Counting Direction: The encoder count direction can be inverted if it does not match the required logical count and travel direction.
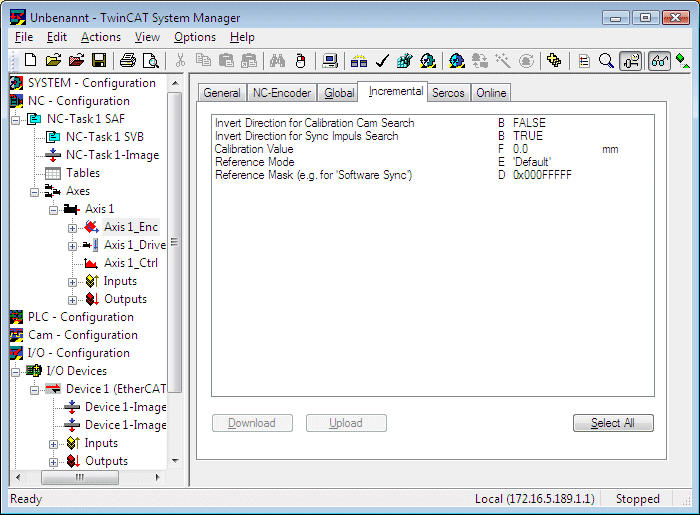
Reference Mode : Referencing mode as described above (Plc CAM, Hardware Sync, Hardware Latch Pos, Hardware Latch Neg, Software Sync). The default mode corresponds to Plc CAM mode.
The Reference Mode parameter is used to specify the type of reference event (physical or logical event) for the referencing process. Depending on the parameterized reference mode, during the referencing procedure either the hardware property of the drive or encoder (e.g. hardware latch) is used, or the reference event is exclusively detected within the control, i.e. without further hardware reference.
Reference Mask: The reference mask parameterizes overflow detection for Software Sync reference mode. It is less or equal the encoder mask and defines an encoder value range, which is part-absolute. Examples include the bit width of a motor revolution or the bit width of a sine period in a sine/cosine encoder. Software Sync therefore always detects the same overflow position in a part-absolute encoder system.
Calibration Value: Reference position to which the axis position is set after homing.
Invert Direction for Calibration Cam Search: The parameter inverts the axis travel direction for searching the referencing cam during homing. The standard direction is negative, i.e. towards the axis coordinate system origin.
Invert Direction for Sync Impuls Search: The parameter inverts the axis travel direction for searching the sync pulse during homing.