With the TwinCAT software oscilloscope
Parameterization of the IDNs P-0-0150 / P-0-0180
![]() | Feedback system 1 or 2 The diagnostic message FA49 applies to both feedback systems 1 and 2. You can find out which feedback system is currently affected by pointing the mouse cursor at the diagnostic message in the TCDriveManager. A tool tip will then appear showing the faulty feedback system. The IDN P-0-0150 described below applies to feedback system 1. The IDN P-0-0180 applies to feedback system 2 and has the same structure as P-0-0150. |
Open the System Manager and select the servo drive (1) which is generating the error. Open the TCDriveManager (2) and select the faulty feedback (4) in the affected channel (3). In the IDN "P-0-0150" (5) under the "Sin / Cos" parameter (6) open the value range (8) under the Parameter "SinCos 1Vss monitoring". Four options appear.
|
0 = Error monitoring (full error monitoring)
1 = Error monitoring and Sin/Cos logging (full error monitoring and logging of sin/cos signals)
2 = Error monitoring (only wire break detection) and Sin/Cos logging (only wire break detection and logging of sin/cos signals)
3 = Error monitoring (only wire break detection)
To log the Sin/Cos signals, select either 1 or 2.
Whether to select option 1 or 2 should generally be decided depending on the application. However, there are two rough indications for making the choice:
If the faulty axis can no longer be used because the error always occurs immediately, then you need to select the "2 = (only wire break detection and logging of sin/cos values)" option so that the error can occur and be logged.
If the faulty axis can be operated because the error only occurs sporadically, then you can select "1 = (full error monitoring and logging of sin/cos values)" or "2 = (only wire break detection and logging of sin/cos values)" so that the error can always be logged.
| |
Warning, risk of injury from uncontrolled movements! If a faulty axis is used then this axis may make uncontrolled movements. Make sure that no one is in the machine's traversing range. |
In many cases the faulty axis can also be moved manually and this option should be used preferentially for safety reasons.
Adding the debug pointer to the Startup list
In order for the sin/cos signals to be logged, the relevant debug pointers must be added to the AX5000 Startup list. Call the Startup list in the TCDriveManager using the button (9) and click on "Add" (10). A window opens with a list of parameters including P-0-1006 to P-0-1010 (11).
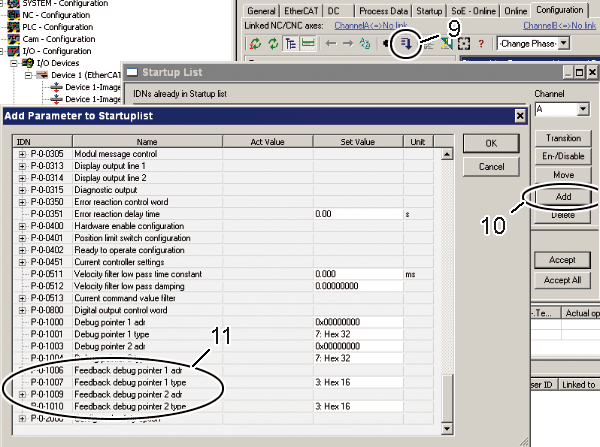
The IDNs need to be parameterized before being added to the Startup list. The IDNs P-0-1006 and P-0-1007 denote sine signals, the IDNs P-0-1009 and P-0-1010 cosine signals; the structures are the same for sines and cosines.
For the IDN "P-0-1006" under "Addr" select the address "0xA000 Sin/Cos ChA: Sin (Int16)" (12).
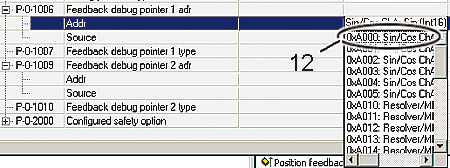
Under "Source" select the faulty feedback system, where "0: Front" refers to the feedback system on the front of the AX5000 and "1: Option" refers to the feedback system on the AX5701 / 02 option card.

For the IDN "P-0-1007" select the option "2: Decimal 16".

You now need to repeat the procedure with the IDNs "P-0-1009" and "P-0-1010". For the IDN "P-0-1009" under "Addr" enter the value "0xA001: Sin/Cos ChA: Cos (Int16)".
Select the four IDNs and press "OK" so that the IDNs are entered in the Startup list.
Activate configuration
In the TCDriveManager (14), click in the tree on "Process Data/Operation Mode". A new window opens where, under "AT or MDT", you select "AT" (16). Next highlight the two IDNs "P-0-1008" and "P-0-1011" (17) and move them into the "Parameter for Process Data" window by clicking on the ">>" button (18).
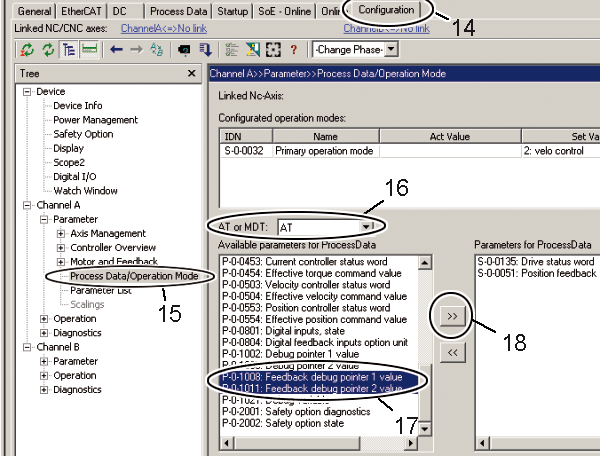
Under the relevant EtherCAT Device (19), activate the ADS Server (20). Now check the boxes beside "Enable ADS Server" and "Create symbols" (21). The "Port" (22) is entered automatically.
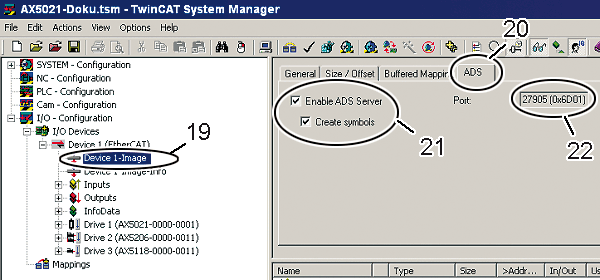
Start "TwinCAT Scope2" and check whether the amplitude values are permissible. The scaling factor is 1 / 46602.