Asynchronous motors
With the AX5000 you have the possibility to implement a good positioning drive with an inexpensive standard motor in combination with a low-cost incremental encoder.
Linear
Linear asynchronous motors are not supported at present.
Rotary
1. Motor selection
You can either choose an existing motor (1) or generate parameters for a new motor (2). After the selection, click "OK". (3) to go to the next menu
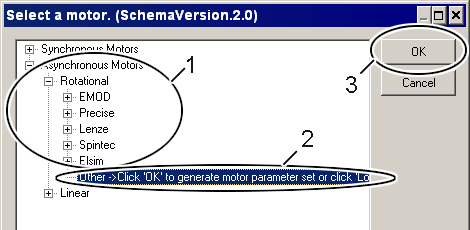
2. Characteristic motor data
In the next menu characteristic motor data are entered or selected. Expert mode (9) is not currently supported. Parameters (4) and (5) are preset; you do not need to change them. You can enter a new motor vendor or select an existing motor vendor in parameter (6). A new group is generated in parameter (7) to suit the motor. If you wish to conform to the structure of the motor database, name the group according to the nominal speed of the motor. Enter the exact type designation of the motor in parameter (8). Check your entries and then click "Next" (10) to move to the next menu.
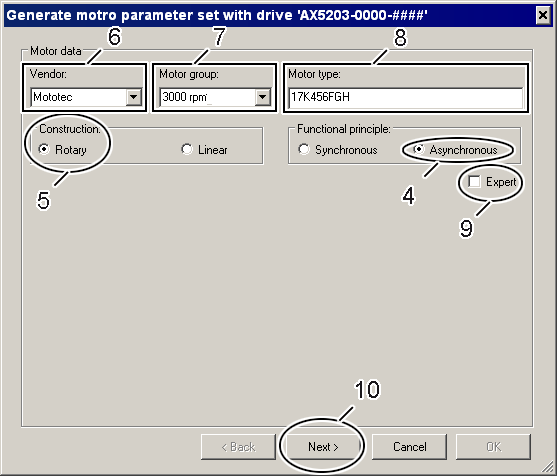
3. Basic motor data
The basic data are subdivided into three categories: "Basic" (1); "Temperature:" (2) and "Brake" (3).
Basic (1):
![]() | It is essential to observe the maximum permitted du / dt of the motor winding! |
a) Connection type: star or delta connection. If you wire and operate the motor in a star or delta connection, please note that the nominal motor current changes along with the nominal motor voltage and that the AX5000 can supply a maximum nominal voltage of 480 V. Please refer to the motor documentation or name plate for the permissible motor voltages and currents for star and delta connection.
b) The derating is dependent upon your application. Derating is the difference between the effective channel nominal current and the nominal motor current in %. Example: nominal motor current = 4 A; effective channel nominal current = 3 A -> derating = 25%.
c) The ratio of Ip to In (overload factor) is set to 1.5 by default and must be checked against the motor documentation or name plate.
d) The nominal current must be adjusted in accordance with the type of connection and checked against the motor documentation or name plate.
e) The maximum motor speed is dependent upon the mechanical properties and the maximum rotary field frequency of the AX5000. Please observe the M / f curve and the field weakening according to the motor documentation.
f) The nominal voltage must be adjusted in accordance with the type of connection and checked against the motor documentation or name plate.
g) The nominal speed is dependent upon the number of pole pairs and the nominal frequency and must be checked against the motor documentation or name plate.
h) The nominal frequency is set to 50 Hz by default and must be checked against the motor documentation or name plate.
i) The power factor (cos phi) is set to 0.8 by default and must be checked against the motor documentation or name plate.
Temperature (2):
k) The type of motor temperature monitoring used and the AX5000 input used must be selected.
![]() | For further information on the combinations you intend to use please contact the Beckhoff applications department. |
m) The temperature at which a warning is output is set to 80 °C. This parameter is effective only for KTY sensors.
n) The temperature at which the motor is switched off is set to 140 °C and must be checked against the motor documentation or name plate. This parameter is effective only for KTY sensors.
Brake (3):
o) The type of motor brake used must be selected and checked against the motor documentation or name plate.
Double-check all entries and click "Next" (4) to move to the next menu.
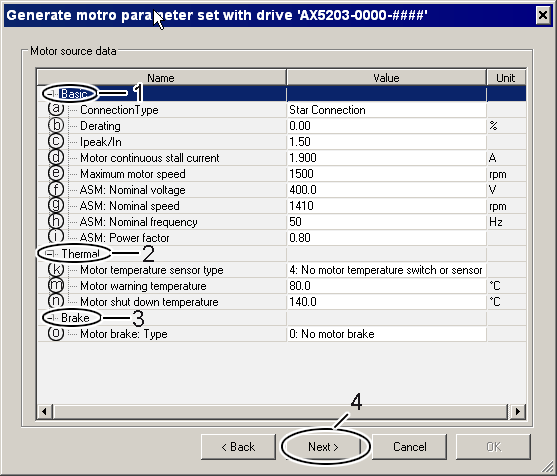
4. Summary
The motor data entered and the data calculated from them are displayed in this window. Please check ALL parameters once more for plausibility and click "OK" (5) to move to the next menu.
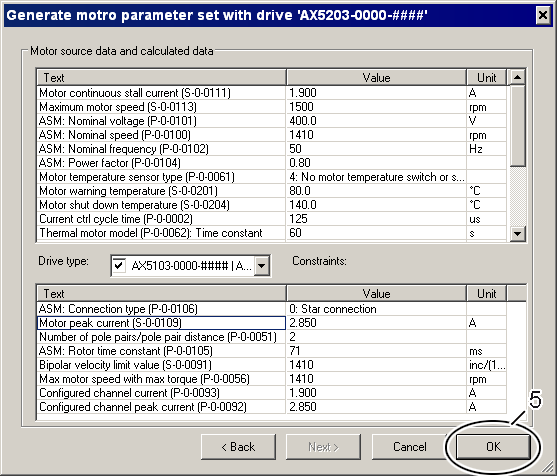
5a. Default storage folder for self-generated motor data sets
The default storage folder for user-generated motor datasets is called "CustomerGenerated" (1), and the suggested file name (2) corresponds to the motor type entered above (see "Characteristic motor data"). This storage folder has the advantage that you can find your self-generated motor data sets at a glance; however, they are not included in the above list above under 1. ‘Motor selection’, but are only visible if you click the ‘Load’ button at the bottom right under 1. ‘Motor selection’. The suggested name designates only the XML file of the motor data set. For the purposes of displaying in the lists, the XML file is read and the corresponding identifying motor data ("Vendor", "Motor group" and "Motor type") are listed as a selection.
To save your data, click on "Save" (4), which then takes you to the last menu.
If your self-generated motor data sets are to be listed directly in the above list under 1. "Motor selection", click on the symbol (3) to open the "MotorPool" folder.
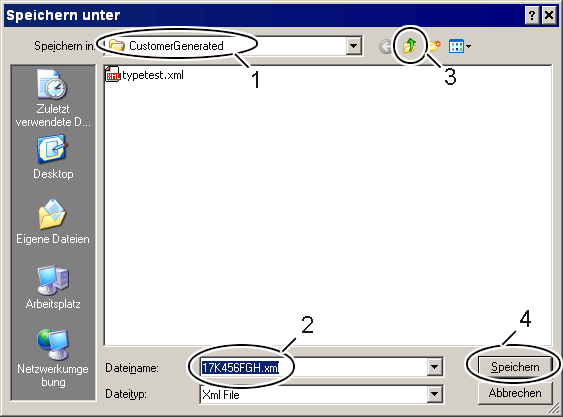
5b. Default storage folder for the motor data sets from the Beckhoff motor database
The default storage folder for the motor data sets provided is called "MotorPool" (4). All motor data sets from the Beckhoff motor database are saved here in the form of XML files. We recommend that you assign a unique file name to your self-generated motor data set so that you can identify it (5):
Customer = Name of your company
Mototec = The name (Vendor) you assigned under 2. "Identifying motor data"
3000 = The motor group (Motor group) you assigned under 2. "Identifying motor data"
17K456FGH = The motor type (Motor type) you assigned under 2. "Identifying motor data"
Of course, you can also assign an arbitrary file name. The assigned name designates only the XML file of the motor data set. For the purposes of displaying in the lists, the XML file is read and the corresponding identifying motor data (‘Vendor’, ‘Motor group’ and ‘Motor type’) are listed as a selection.
You create one XML file for each motor data set; the motors from the same motor group of a vendor are always summarized in the XML files for Beckhoff motor data sets.
To save your data, click on "Save" (6), which then takes you to the previous menu.
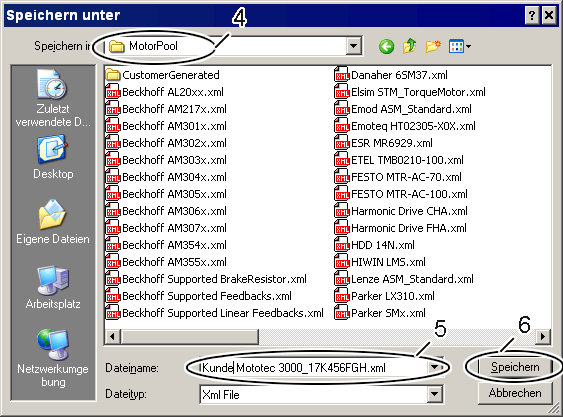
6. Mains voltage and extra settings
This window also appears when you select an existing motor data set (synchronous motor or asynchronous motor). You can adapt the following entries at any time.
a) You can select one of the pre-defined mains voltage variants or you can specify one of your own.
b) Enter the mains voltage (only possible if no mains variant was selected under a)).
c) Enter the upper tolerance of the mains voltage (only possible if no voltage was selected in a)).
d) Enter the lower tolerance of the mains voltage (only possible if no voltage was selected in a)).
e) + f) Phase monitoring is only useful for a 3-phase supply network. Switch phase monitoring on or off (only possible if no voltage was selected in a)).
g) Use this setting to enable automatic transfer of the resolution of the encoder and the scaling factor from the AX5000 to the NC. (Only required if the motor was integrated via an NC axis).
h) The cycle time of the current controller is 125 μs.
i) Selection of the ASM connection type. If you have generated the motor data set, you can only select the type of connection entered under 3. "Basic motor data –a)". If Beckhoff has generated the motor data set, you can choose between star connection and delta connection.
k) Selection of the ASM control mode. If you select "U/f control", only open-loop operation of the motor is possible; the AX5000 then acts like a servo drive. If you select "i-control with feedback", closed-loop operation of the motor is possible, but the motor must be equipped with a feedback system. Click on "OK" (1) to complete the procedure.
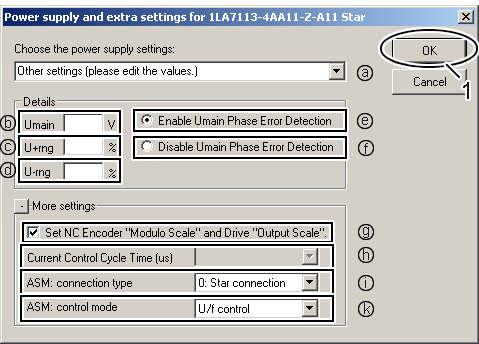
Open-loop
If open-loop operation of the motor is desired, you can influence the operating behavior with the following parameters.
Interdependence between the type of connection of the motor, the speed and the nominal output current of the AX5000
Example motor:
Asynchronous motor with nominal voltage 230 V and nominal current 6 A at 50 Hz for delta connection or nominal voltage 400 V, nominal current 3.5 A at 50 Hz for star connection
If your application requires speeds above the nominal speed (1), this requirement can be realized without having to use a larger motor:
The AX5000 can provide 400 V channel output voltage and thus operate the asynchronous motor in delta connection up to 87 Hz (2) without field weakening occurring, i.e. with nominal torque. You only need to note that a nominal current of 6 A is required.
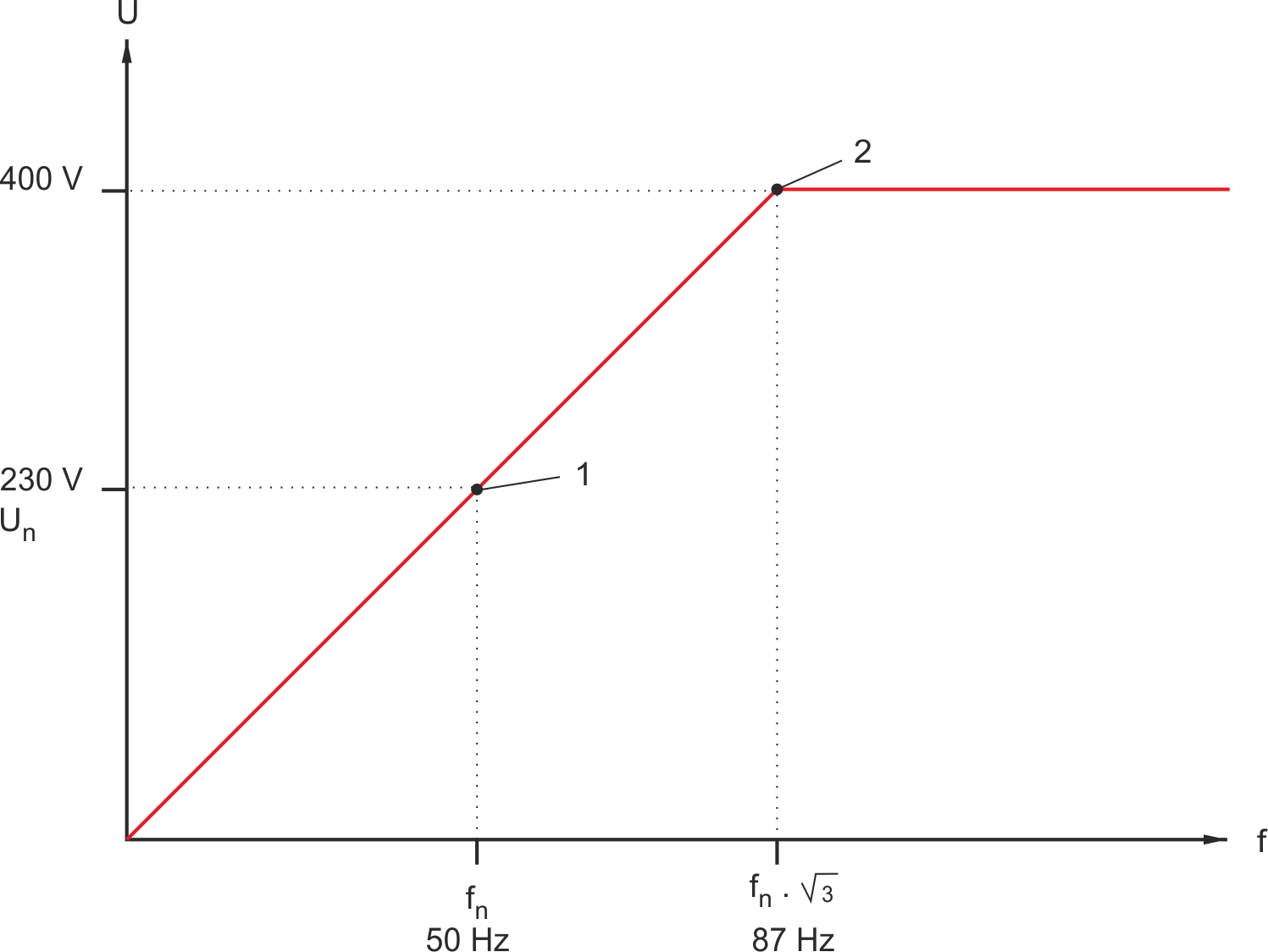
Boost voltage
The operation of an asynchronous motor with a linear U/f characteristic curve results in a weakening of the torque in the lower speed range due to the dominant resistive component. The standstill torque is zero without a boost voltage. Furthermore, the asynchronous motor requires a certain time after the current is applied in order to build up the magnetic field on the rotor and, hence, to generate the magnetic force or the torque. If your application can not tolerate this delay, there is a possibility to reduce this time delay via the so-called "boost voltage", which "premagnetizes" the rotor. With "premagnetization" a magnetic field is created in the rotor even though the rotor is not moving. Torque is hence immediately available to rotate the rotor shaft if a target speed is specified. The interdependence between the boost voltage, speed and torque is illustrated in the graphic below on the basis of an example motor. The influence of the boost voltage on to the torque is clearly visible at low speeds.
Example motor:
Nominal speed: 1410 min-1
Nominal torque: 10.2 Nm
Breakdown torque: 28.6 Nm
Starting torque: 25.5 Nm
Power factor: 0.78
Efficiency: 0.79
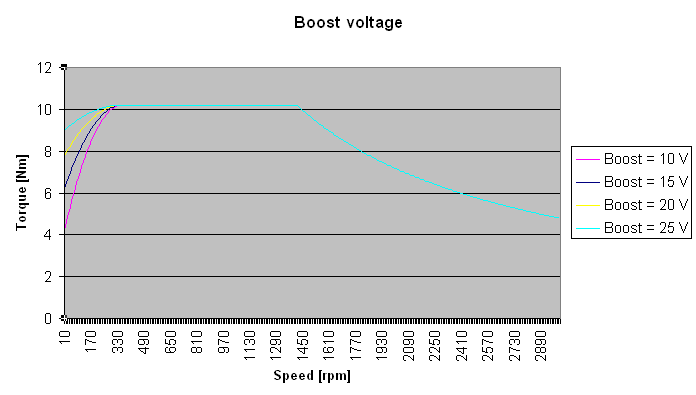
The boost voltage is parameterized in the IDN-P-0-0103. Most applications will be covered by the default setting of 10 V.
Notice | |
Attention: destruction of the motor In an asynchronous motor without an external fan, the motor temperature must be monitored in the lower speed range when boost voltage is used. If necessary, you can change the boost voltage online. |
Settings for ramping up and down
For the controlled operation of the asynchronous motor, it depends on the application which values you have to set for the ramping.
Ramping up is parameterized in IDN S-0-0136 and ramping down in IDN S-0-0137.
Closed-loop
If closed-loop operation of the asynchronous motor is desired, you must select the feedback system used in the motor in the TCDM.
Feedback
Start the TCDM and click the entry (2) under the relevant channel (1) in the tree; the motor/feedback configuration appears in the TCDM working area. Click on the ‘Feedback 1’ (3) field to open the ‘Feedback selection window’. You can view all available feedback systems in the "Feedback selection window".
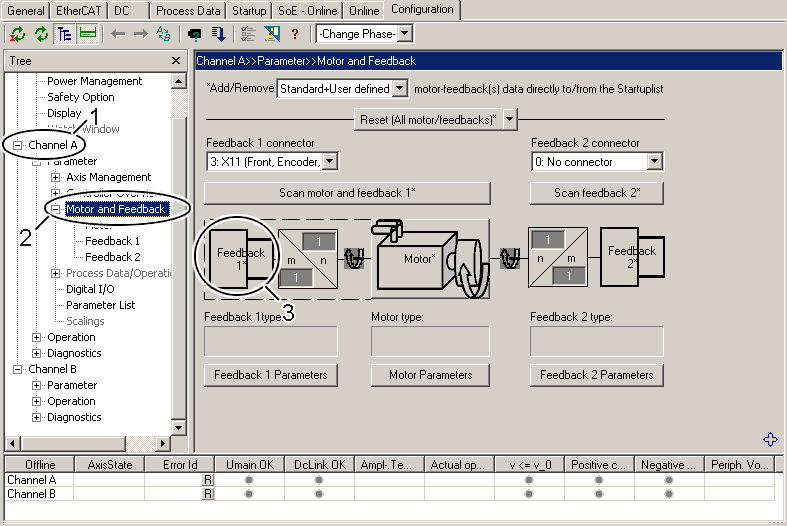
1a. Feedback selection - resolver
Only one of the listed feedback systems can be selected. Either choose the feedback system of an existing vendor or choose a standard feedback system under "Unknown" (1). If your motor is equipped with a resolver, determine the generic parameters of the resolver and select the appropriate resolver type (2). Typical generic parameters for the classification of resolvers are the number of poles "p" and the gear ratio "n". Click on "OK" (3) to complete the procedure.
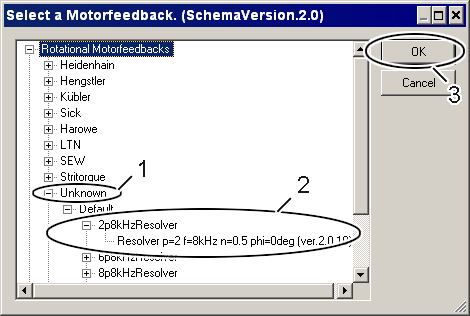
1b. Feedback selection - 1Vpp encoder
You can only select one existing feedback system. Either choose the feedback system of an existing vendor or choose a standard feedback system under "Unknown" (1). If your motor is equipped with a 1Vpp encoder, determine the parameters of the feedback system and select the appropriate encoder (2). Typical parameters for the classification of 1Vpp encoders are the number of lines "s" and the supply voltage "5 V or 5 V fixed". The difference between the two voltage variants is the use of a sense line (5 V). Click on "OK" (3) to complete the procedure.
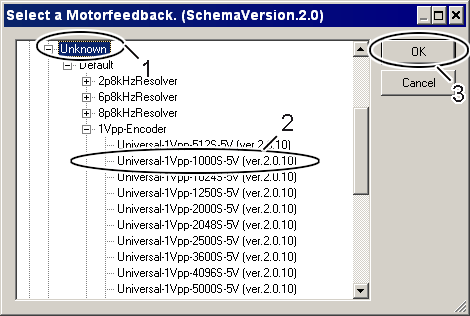
1c. Feedback selection - TTL encoder
You can only select one existing feedback system. Either choose the feedback system of an existing vendor or choose a standard feedback system under "Unknown" (1). If your motor is equipped with a TTL encoder, determine the parameters of the feedback system and select the appropriate TTL encoder (2). Typical parameters for the classification of TTL encoders are the number of lines "s" and the supply voltage "5 V or 5 V fixed". The difference between the two voltage variants is the use of a sense line (5 V). Click on "OK" (3) to complete the procedure.
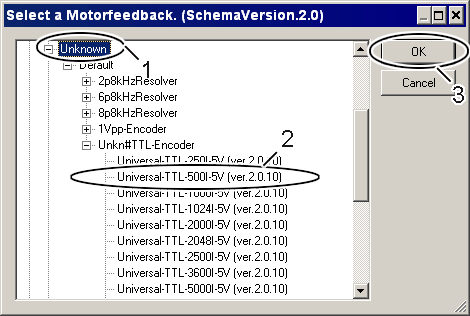
![]() | TTL Encoder! Wire break detection is not supported for TTL encoders. |
Commutation
In asynchronous motors the rotor magnetic field is generated electrically by means of rotor windings, which are energized by the servo drive. For this reason, neither a part-absolute nor an absolute encoder system is required for commutation; wake+shake also does not need to be used. The magnetic field of the stator induces a voltage in the rotor windings. This leads to a current flow in the rotor windings. This in turn generates a magnetic field, which produces a torque.