Configuration of the second encoder
Please refer to the AX5000 system manual on how to connect the encoder.
In the Tc Drive Manager, select the "Feedback 2" page and "Select a Motorfeedback" to select the encoder from the list of supported feedbacks. In the following example, a linear encoder from Heidenhain with EnDat interface and sine-cosine signals is selected:
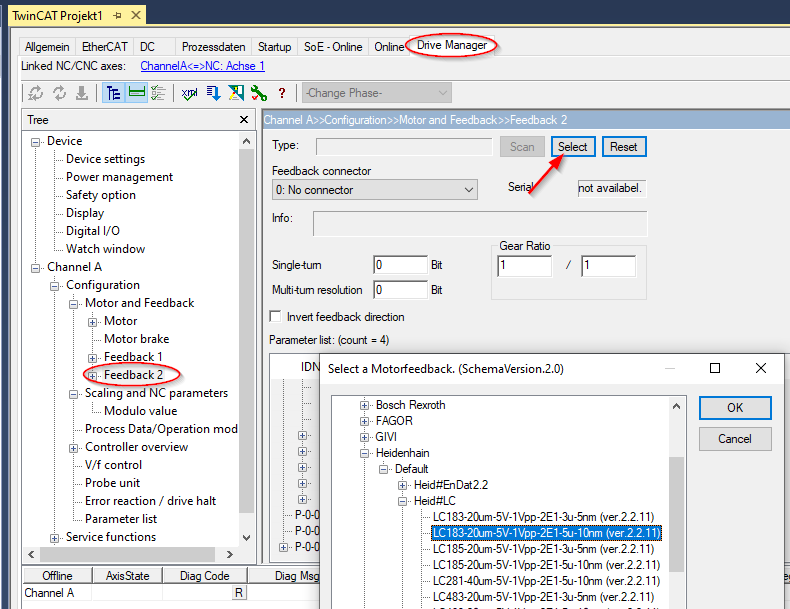
Confirm the message with "OK". The mentioned settings are described below.
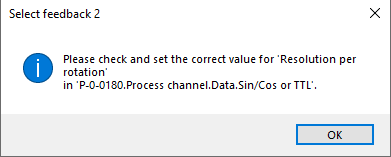
If the correct connector is not set automatically, select it from the list:
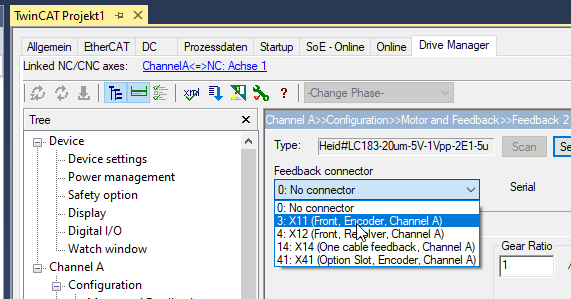
Open the parameter P-0-0180 to get to the entry Process channel/Data/Sin / Cos/:
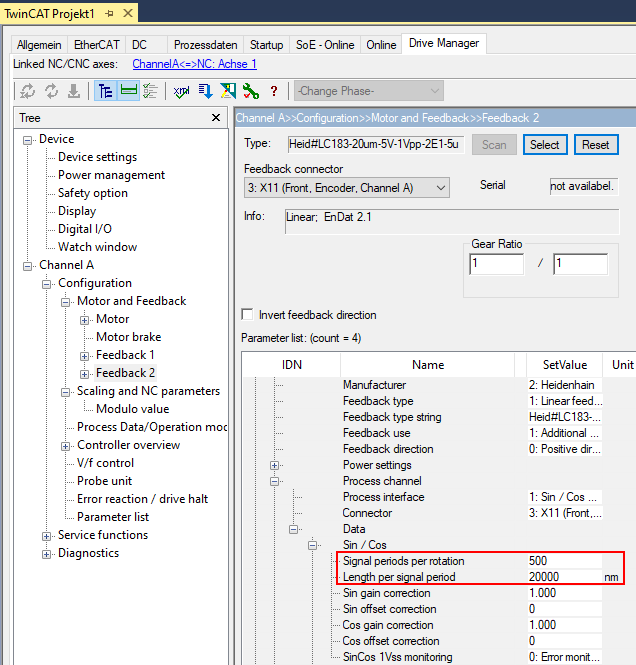
"Length per signal period" is set automatically from the database.
You must select "Signal periods per rotation" so that the product of the two gives the travel distance of the load during one motor rotation.
Example: The motor drives a ball screw with 10 mm pitch.
=> The load moves 10 mm per motor rotation.
Length per signal period = 20000 nm is automatically set from the database.
Signal periods per rotation = 10 mm / 20000 nm = 500
Note: Both parameters must have correct values for both rotary and linear feedback.
Add parameter P-0-0053 to the process image and ensure that the operating mode remains "11_ pos ctrl. feedback 1, lag less".
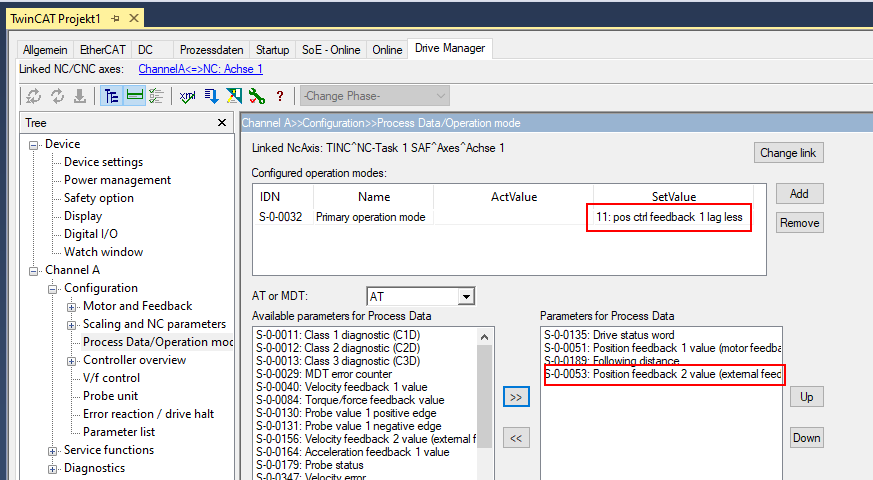
Execute "Activate configuration" for the changes to take effect.