Linking into the System Manager
Because of the automatic mechanisms that are present, it is advisable to begin the configuration by inserting the I/O devices.
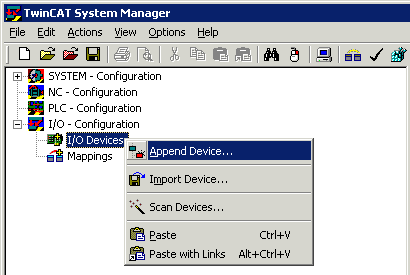
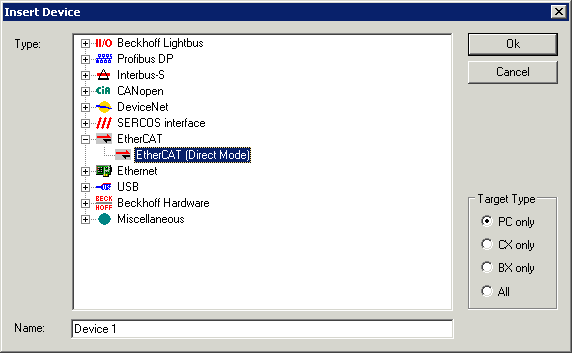
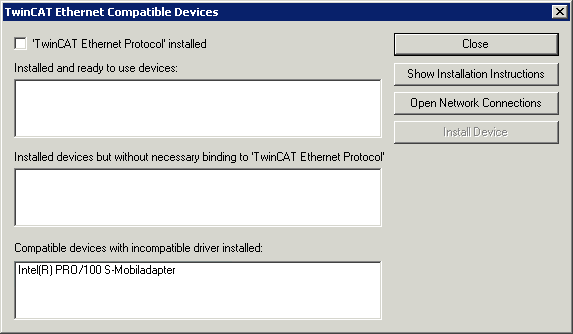
Reference to Information System -> System Manager -> Appendix C
If the master has been properly installed, it appears as a usable device.

The configuration that has been created is then switched into config mode, and a scan is made for connected boxes. Those devices that are connected are addressed by the master in accordance with their sequence in the ring. If an axis is detected, the System Manager offers the option of adding an NC axis and creating the corresponding link.
I/O level: Selecting the process image
Setpoint contents (outputs from the point of view of the master) can be selected as follows: AX2000-B110 Process Data tab under Sync Manager Outputs. The selected PDO can be seen in the PDO assignment window. A new selection is not possible until the configuration that had previously been established is deselected. Both inputs and outputs can be selected in the PDO list window. The content of the PDOs is then displayed in the PDO Content window.
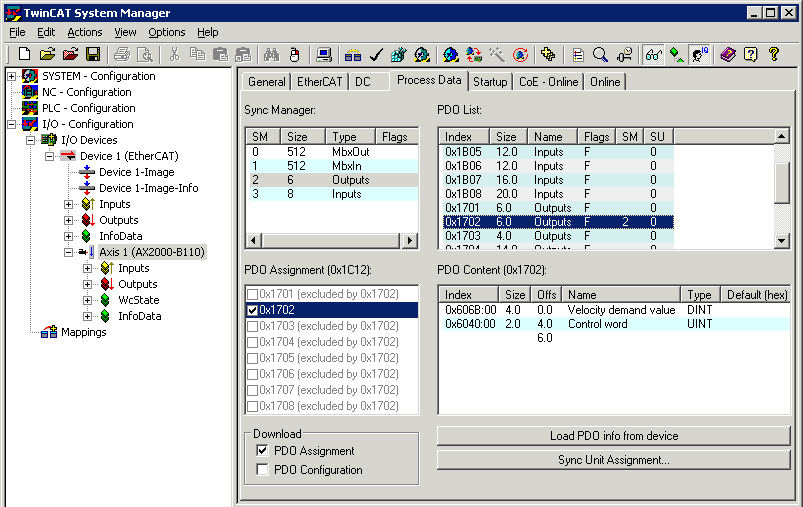
In the default state, the PDO assignment is linked to object number 0x1702 (set values) and object number 0x1B03 (actual values).
Interfaces
Position interface
Address | Description | |
---|---|---|
0x1701 | Position setpoint, control word (6 bytes) | DINT 32 bit position (20 bits/rotation) |
0x1B01 | Actual position value, status word (6 bytes) | DINT 32 bit position (20 bits/rotation) |
Speed Interface (default mapping)
Address | Description | |
---|---|---|
0x1702 | Speed setpoint, control word (6 bytes) | DINT 32 bit speed (rotation/139Inc) |
0x1B01 | Actual position value, status word (6 bytes) | DINT 32 bit position (20 bits/rotation) |
Torque interface
Address | Description | |
---|---|---|
0x1703 | Torque setpoint, control word (4 bytes) | INT 16 bit torque setpoint (peak current -> 3280 Inc) |
0x1B03 | Actual position value, actual torque value, status word (8 bytes) | INT 16 bit torque setpoint (peak current -> 3280 Inc) |
Position, speed, and torque interface with operating mode changeover
Address | Description | |
---|---|---|
0x1704 | Position setpoint, speed setpoint, torque setpoint, operating mode request, control word (14 bytes) | Operating mode request object 0x6060 |
0x1B04 | Actual position value, actual torque value, operating mode feedback, status word (10 bytes) | Feedback of the selected operating mode 0x6061 |
Position and speed Interface with “Torque” extension package
Address | Description |
---|---|
0x1705 | Position setpoint, speed setpoint, additive torque setpoint, torque limit, control word (14 bytes) |
0x1B05 | Actual position value, actual torque value, drive following error, status word (12 bytes) |
Position and speed Interface with “Latching” extension package
Address | Description | |
---|---|---|
0x1706 | Position setpoint, speed setpoint, control word, latch control word (12 bytes) | The latch control word is described in the Some important objects section |
0x1B06 | Actual position value, status word, latch status word, latch position (12 bytes) |
|
Position, speed, and torque interface with operating mode changeover and with “Latching” extension package (not yet implemented!)
Address | Description |
---|---|
0x1707 | Position setpoint, speed setpoint, torque setpoint, operating mode request, control word, latch control word (16 bytes) |
0x1B07 | Actual position value, actual torque value, operating mode feedback, status word, latch status word, latch position (16 bytes) |
Position, speed, and torque interface with operating mode changeover and with the “Torque” and “Latching” extension packages
Address | Description |
---|---|
0x1708 | Position setpoint, speed setpoint, torque setpoint, torque limit, operating mode request, control word, latch control word (18 bytes) |
0x1B08 | Actual position value, actual torque value, drive following error, operating mode feedback, status word, latch status word, latch position (20 bytes) |
Start-up list
The user can save slave-related settings in this region of the configuration. This list is loaded into the servo drive every time there is a transition from the PREOP to the SAVEOP state.
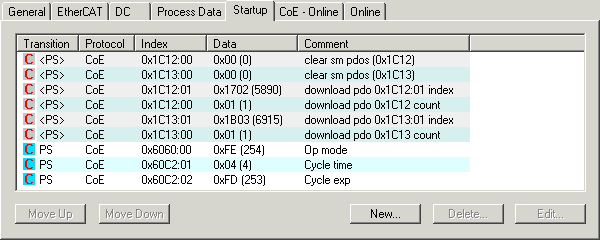
These entries are generated by the System Manager. The first 6 entries save the process image in the Sync Manager. The seventh entry specifies the controller’s operating mode:
Operation mode | Digital speed | Torque, digital | Ext. trajectory |
---|---|---|---|
Value | 0xFE | 0xFD | 0xFA |
The two last entries specify the cycle time. In this case it is 1*10-2 seconds.
NC level
No further settings need to be made after the inputs and outputs have been linked with the Box (AX2000-B110). The typical NC settings for the scaling factor, maximum speed, software limit switches and so forth are to be carried out according to the Information System.