Design of the motors
Beckhoff stepper motors of the AS1000 series are synchronous motors with a large number of poles. They are classified as direct drives. The stepper motors of the AS1000 series are characterized by a high holding torque and very good positioning capability. Thanks to sophisticated control of the stator windings in full-step or micro-step mode, individual steps or partial steps can be executed directly without a feedback system. This feature distinguishes stepper motors from servomotors, thus representing a cost-effective alternative approach. Excessive acceleration and fast load cycles can result in the stepper motor being unable to follow the rotating field and therefore "losing steps". The encoder option can improve matters in this situation.
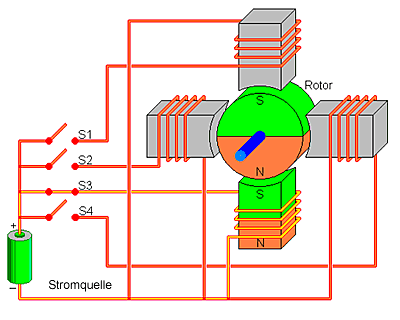
The stepper motor has its highest torque in the lower speed range. At standstill, the stepper motor is characterized by a very high holding torque. In many applications, this eliminates the need for a holding brake. In the Beckhoff stepper motor terminals a suitable current curve can be stored for any speed or load profile. This serves to optimally adapt the thermal load of the motor. Beckhoff stepper motors are used as actuators or auxiliary axes in machine construction and automation applications. In conjunction with the stepper motor output stages and the Beckhoff TwinCAT automation system, this facilitates integration of cost-effective axes into the overall application. In order to simplify the electrical connection, the stepper motors are equipped with pre-assembled plug connectors. Planetary gear units, incremental encoders and pre-assembled connection cables are available as accessories.