Commissioning
![]() | Exemplary commissioning The procedure for commissioning is described as an example. A different method may be appropriate or necessary, depending on the application of the components. |
![]() | Requirements for commissioning Before commissioning the AL8200 MES, the following steps must be completed:
|
The commissioning of the AL8200 MES is to be carried out as follows:
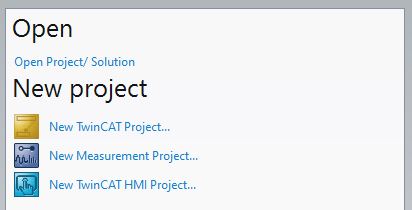
- 1. Create new TwinCAT project
- 2. If connected to target system, scan devices
- 3. Accept message "HINT: Not all types of devices can be found automatically" with "ok"
- 4. Select Ethernet port
- 5. Confirm the scan prompt with "yes"
- 6. AX5000 Motor scan Select "no" button (linear motors cannot currently be scanned)
- 7. Select NC or CNC axis
- 8. Add new project
- 9. Select new Drive Manager 2 project
- 10. Confirm supply voltage query and motor scan with "Continue"
- 11. Click "OK"
- 12. Confirm upcoming message with "OK
- 13. Open the relevant channel in the Solution Explorer under the Drive Manager 2 project
- 14. The Drive Manager 2 opens
- 15. Select the AL8000 linear motor under "Motor/Select
- 16. In the "Load" submenu, parameterize and save feedrate and mass
- 17. Select feedback (Beck#AL8200MES-5V-1Vpp)
- 18. Determine direction of rotation and commutation angle in parameter P-0-0166 (see also AX5000 System Manual, chapter 9.6.2)
- 19. "Equal directions" / "Yes"
The value for "Commutation position difference" should now lie within the range: 355...360 = 0...5. - 20. Set "Commutation mode" in parameter P-0-0150 to "Commutation offset 0 deg (2)"
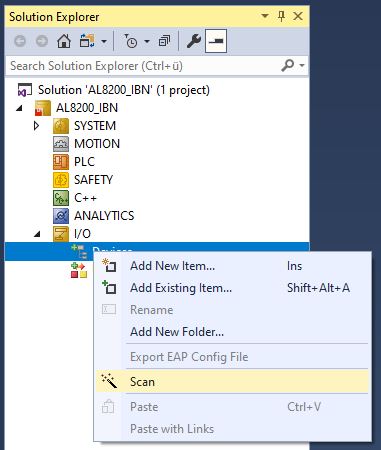
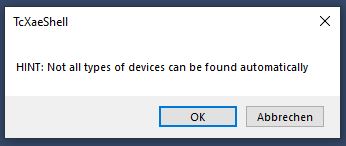
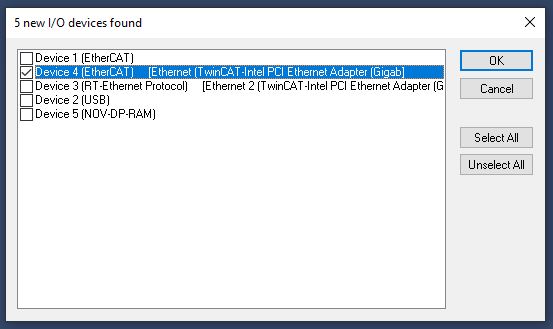
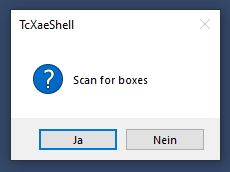
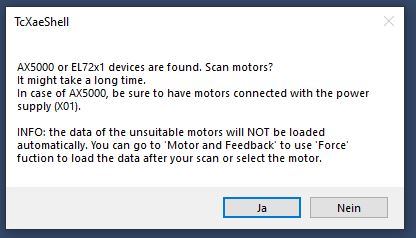
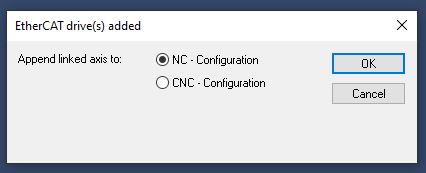
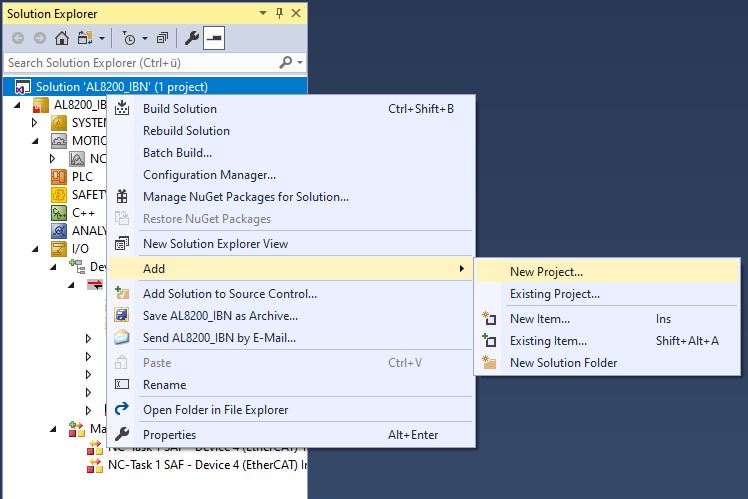
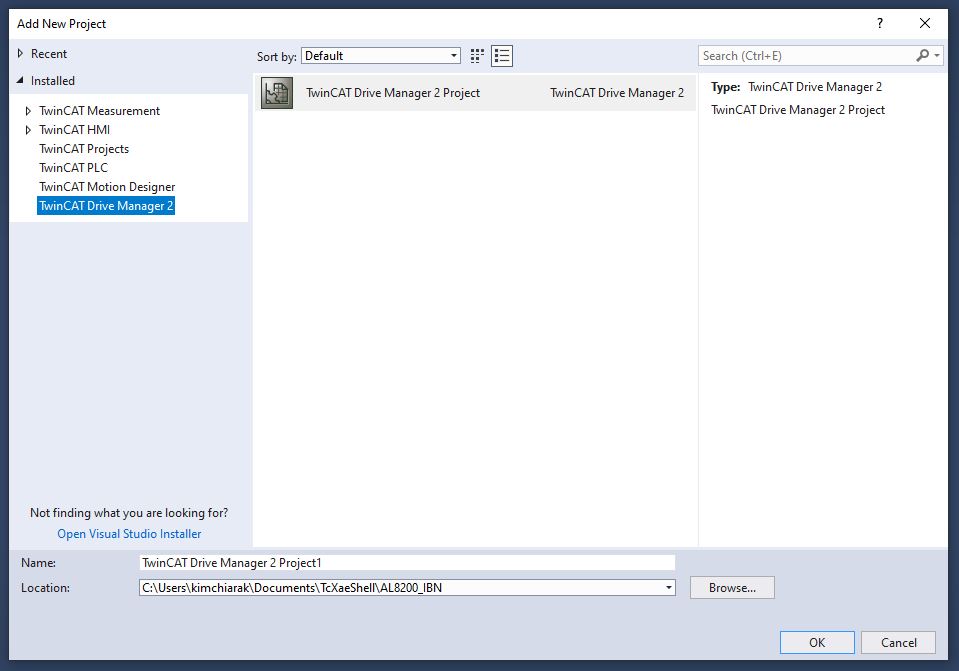
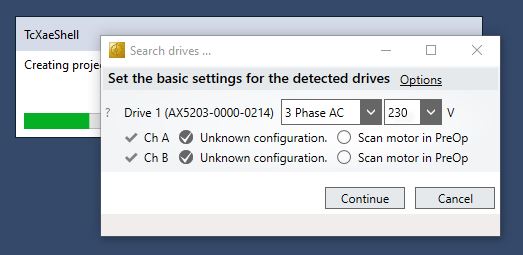
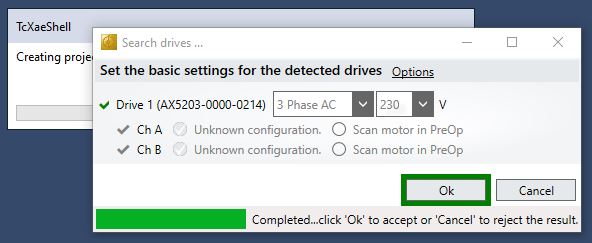
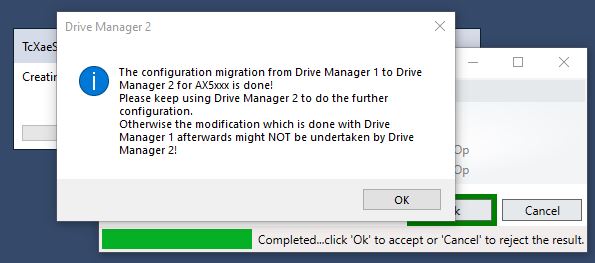
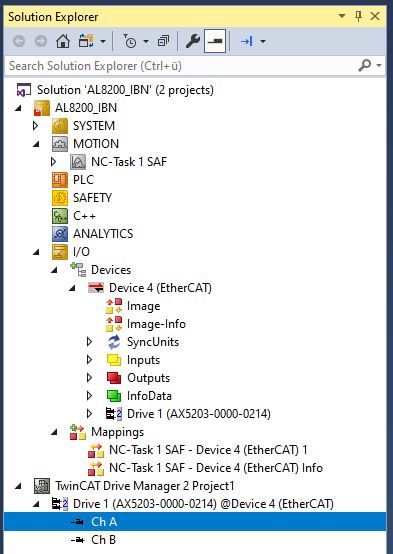
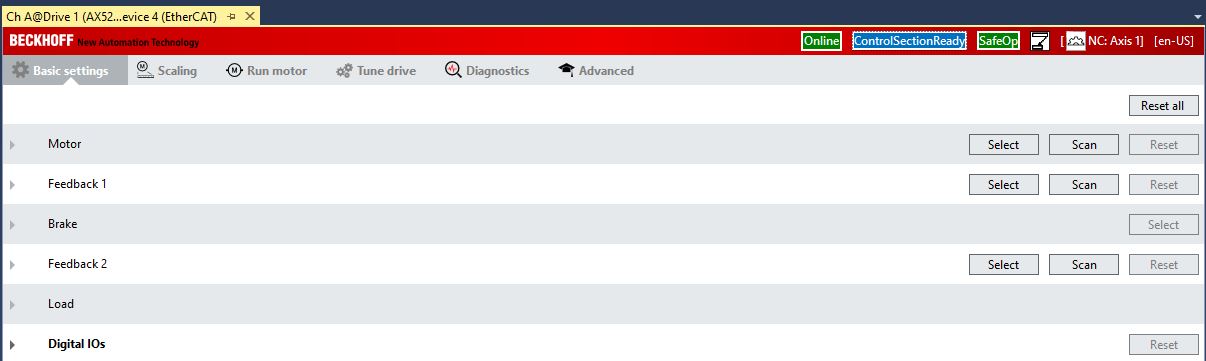
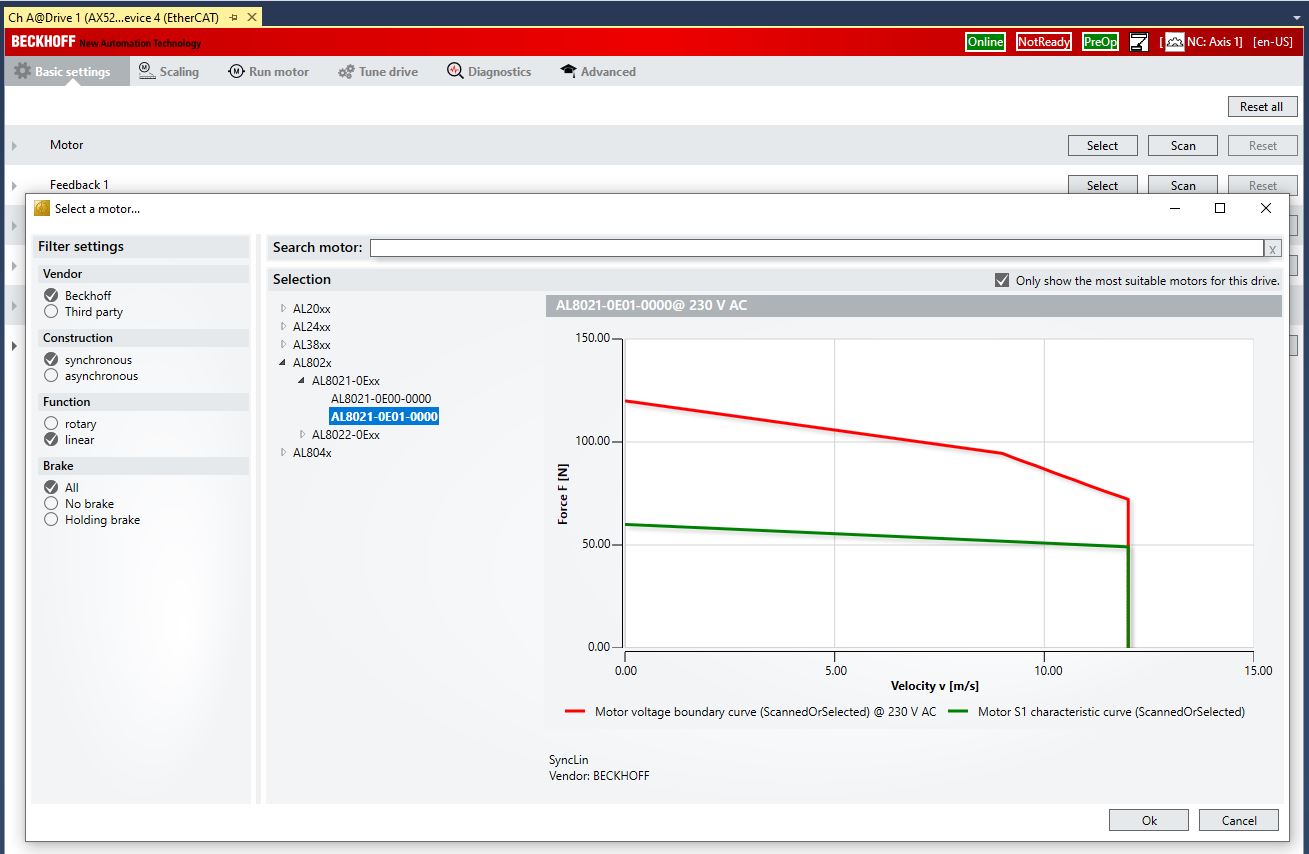
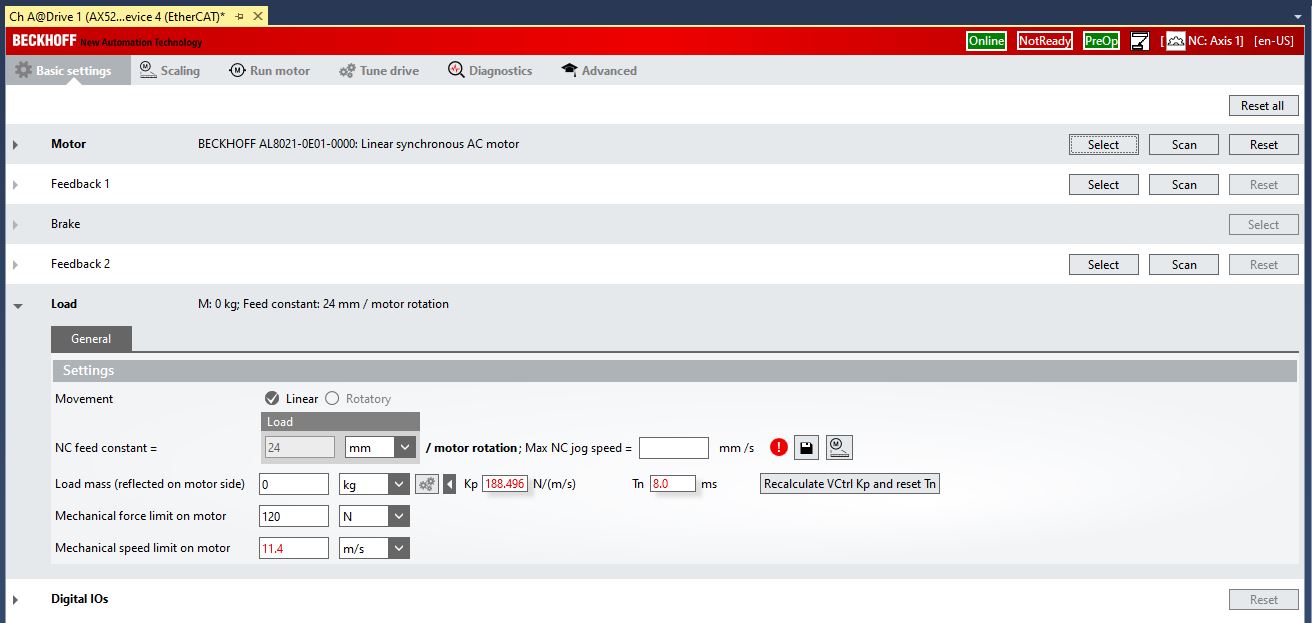
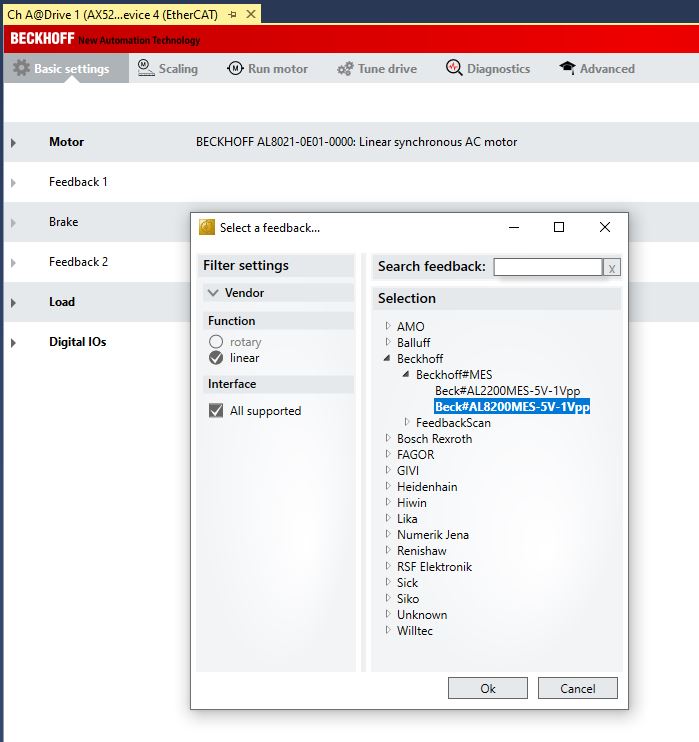
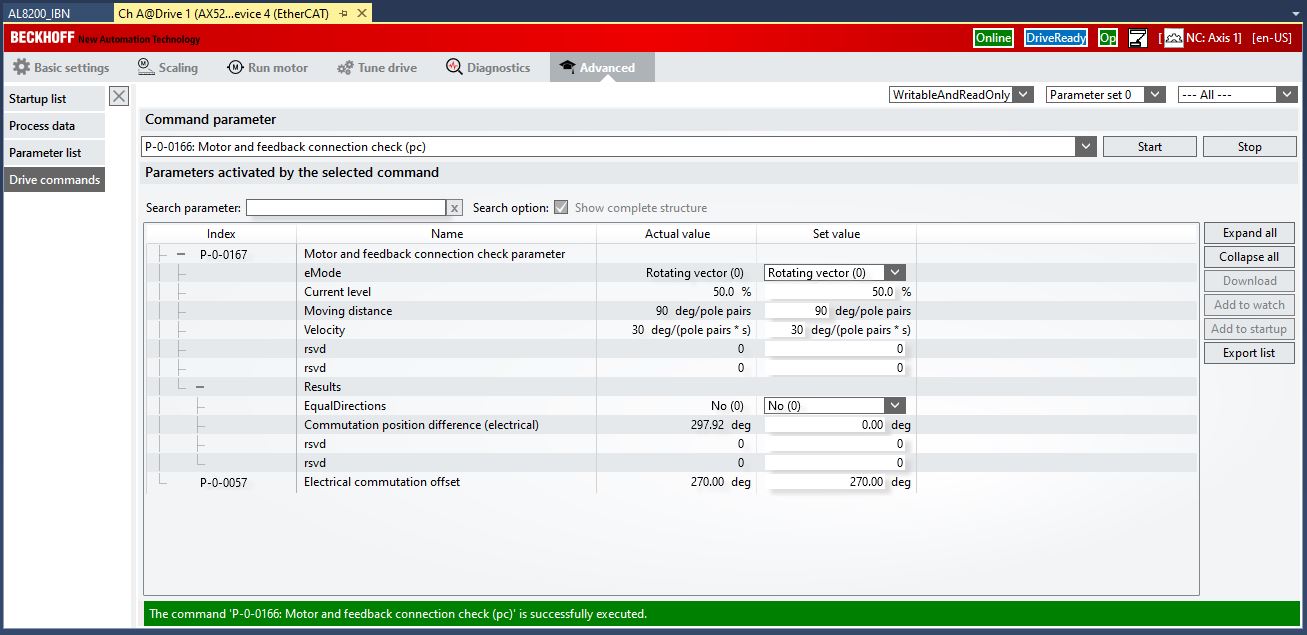
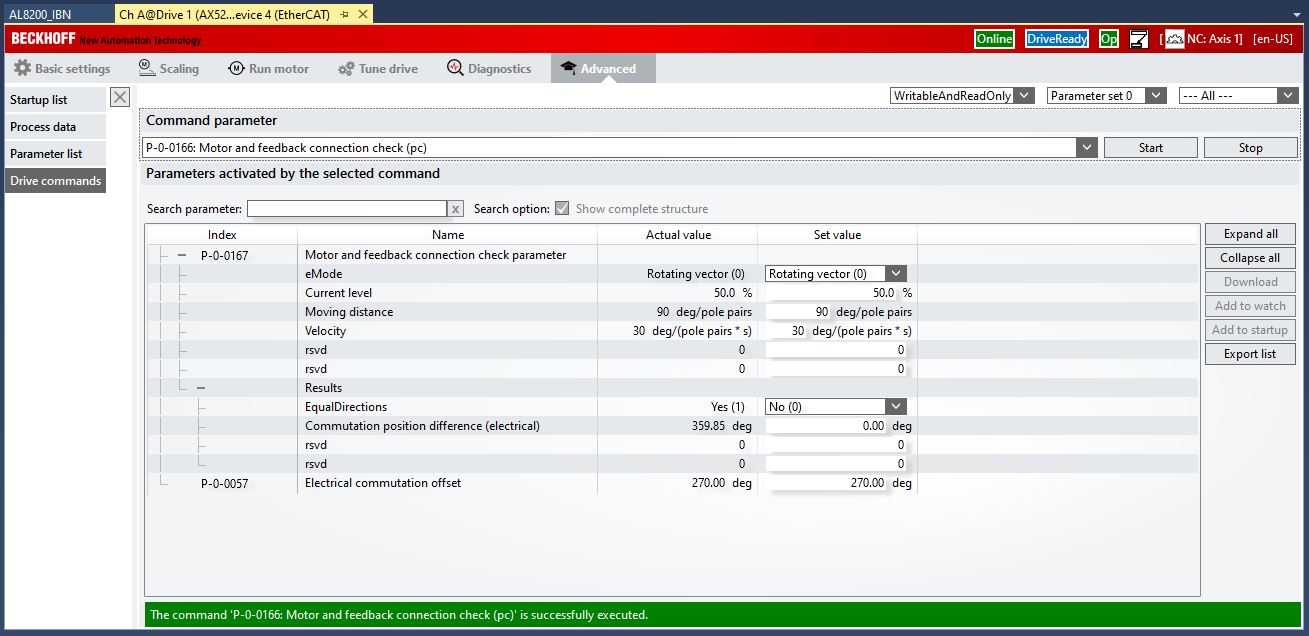
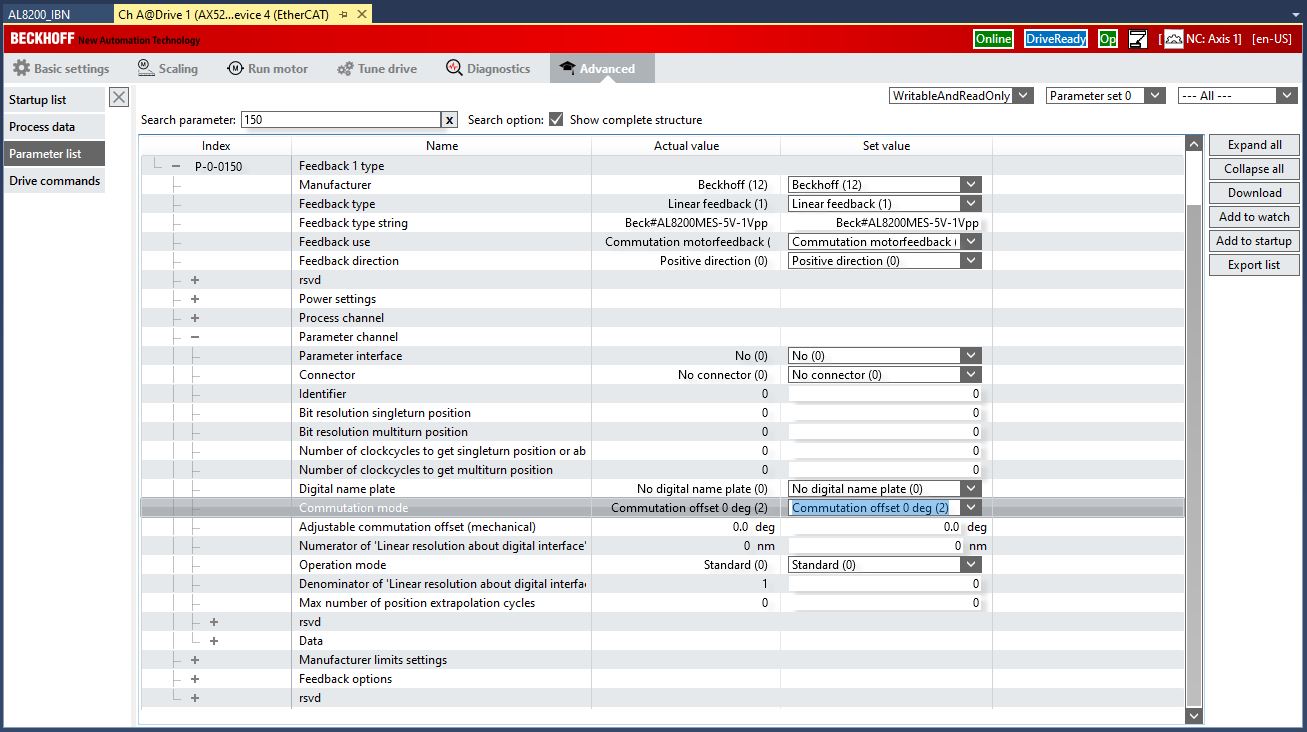
The axis can then be moved, e.g. for controller optimization.