Schrittmotor-Achsen
Die Schrittmotor-Achse wird in der Basisversion ohne physikalischen Encoder betrieben. Dies bedeutet, dass es keine wirkliche physikalische Rückkopplung der Istposition gibt. Durch das Arbeitsprinzip des Schrittmotors ist die Anzahl der ausgeführten Schritte exakt gleich der Anzahl der ausgegebenen Pulse und somit kann der Schrittzähler als Pseudo-Encoder benutzt werden. Dabei ist zu beachten, dass dieser Zusammenhang bei Überlastung des Motors verloren geht. Das nachfolgende Diagramm zeigt den Zusammenhang zwischen Drehmoment und Abdrängwinkel.
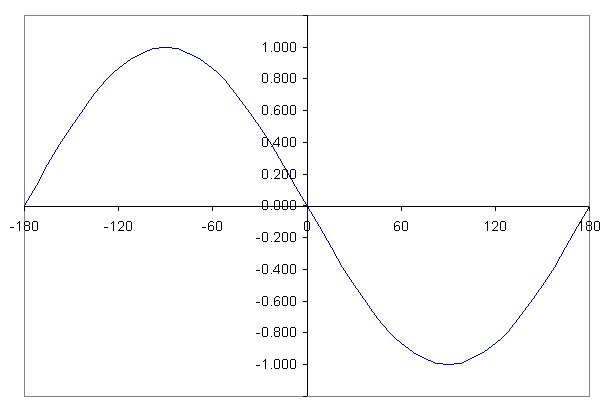
Die Winkelangaben beziehen sich auf einen vollständigen Impulszyklus. Bei einem Motor mit 200 Pulsen bei Vollschritt-Betrieb entspricht der dargestellt Bereich also 3.6 Grad an der Motorwelle.
Wenn der Motor im Stillstand oder in Bewegung ein Drehmoment aufbringen muss, wird der Rotor gegenüber der drehmomentfreien Idealstellung um einen entsprechenden Winkel abgedrängt. Dies entspricht dem Verhalten einer nichtlinearen Feder im Antriebsstrang. Abgesehen von der daraus resultierenden Positionsabweichung des angetriebenen Maschinenteils ist dies unproblematisch, solange der obere oder untere Scheitelpunkt nicht erreicht wird. In diesem Fall sinkt das Drehmoment des Motors ab und das weiterhin anstehende Lastmoment wird den Motor immer weiter abdrängen. Der Motor ist dann nicht in der Lage, zum korrekten Winkel zurückzukehren und durchläuft einen vollständigen Polzyklus. Erst dann besteht die Chance, dass die Magnetfelder von Rotor und Stator stabil ineinander einrasten. Dies wird jedoch nur dann zu einem stabilen Verhalten führen, wenn das Lastmoment zu diesem Zeitpunkt deutlich unter dem Drehmoment des Motors liegt. In diesem Fall hat sich der Motor dann um einen vollständigen Zyklus versetzt und muss neu referenziert werden. Allerdings ist diese Situation ohne eine entsprechende Sensorik nicht erkennbar.
Eine völlig andere Situation tritt ein, wenn das Lastmoment durch das Versetzen um einen Polzyklus nicht praktisch unmittelbar nachlässt. Dies ist vor allem dann der Fall, wenn das Lastmoment aus der Beschleunigung entsteht. Jetzt wird der Motor nicht am nächsten stabilen Punkt mit einem Versatz von einem Polzyklus einrasten, sondern diesen Punkt ebenfalls durchlaufen. Er verliert jetzt gegenüber dem aufgeprägten Statorfeld immer mehr an Geschwindigkeit und durchläuft jeden weiteren Impulszyklus ohne dabei ein Netto-Drehmoment zu erzeugen. Dies führt dazu, dass der Motor unter erheblicher Geräuschentwicklung austrudelt. Am Ende durchläuft das Fahrprofil einen Bereich absinkender Impulsfrequenzen. Abhängig vom Lastmoment wird der Motor mehr oder weniger kurz vor dem Ende des Profils ruckartig beschleunigen und dem Rest des Profils folgen. Letztlich hat er dann jedoch einen mehr oder weniger großen Teil des Profils und somit des Weges nicht ausgeführt. Auch dies ist ohne eine entsprechende Sensorik nicht festzustellen.
Bei der Auslegung eines Schrittmotors ist besonders darauf zu achten, dass die Drehzahl einen starken Einfluss auf das verfügbare Drehmoment besitzt. Das nachstehende Diagramm zeigt den Zusammenhang für einen typischen Motor.
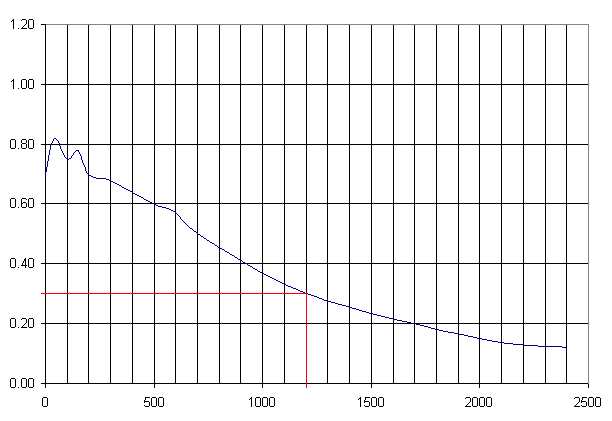
Der Motor hat neben dem Lastmoment aus dem Prozess auch die Momente aufzubringen, die durch die Dynamik des Fahrprofils entstehen. Wenn das Gesamt-Moment wie im Beispiel 0.3 Nm beträgt, darf dieser Motor also maximal mit einer Drehzahl von 1200 RPM betrieben werden. In der Praxis sollte jedoch unbedingt eine angemessene Momentenreserve eingeplant werden.
Konfiguration der Schrittmotorachse
Achs-Typ: Kontinuierliche Achse (inkl. SERCOS)
Encoder-Typ: Encoder an KL5051/KL2502-30K/KL2521
Controller-Typ: z. B. Positionsregler P
Drive-Typ: Antrieb an KL4XXX/KL2502-30K/KL2521
Referenzieren
Wie üblich muss das digitale Referenziernockensignal mittels der SPS in das Achsinterface zur NC (PlcToNc-Achsstruktur) gespiegelt werden. Hierbei gilt der übliche Ablauf für das Referenzieren einer Achse, wobei auf die Hardwareeigenschaft „Latchen einer Position“, veranlasst durch einen Syncimpuls, verzichtet werden muss. Stattdessen dient beim Herunterfahren vom Referenziernocken die fallende Flanke als örtliches Ereignis, um eine Referenzposition zu ermitteln. Die Genauigkeit des Referenziervorgangs kann durch Reduzierung der Geschwindigkeit beim Herunterfahren vom Nocken beliebig erhöht werden (maximal mögliche Genauigkeit beträgt ein Motorschritt).
![]() | Im Unterschied zu einer Achse mit Analog-Sollwertausgabe, z. B. über eine KL4032, muss beim Betrieb eines Schrittmotorleistungsteils an einer KL2502-0010 oder -3020 oder KL2521 die Klemme entsprechend dem Einsatzfall parametriert werden. |
Parametrierung der KL2502-0010 oder -3020
Diese Varianten der KL2502 unterscheiden sich in der Hardware von der Basis-Version. Die dadurch erzielte Erhöhung aller internen Arbeitsfrequenzen macht einen erweiterten Arbeitsbereich zugänglich, wird jedoch derzeit in der KS2000 Software nicht berücksichtigt.
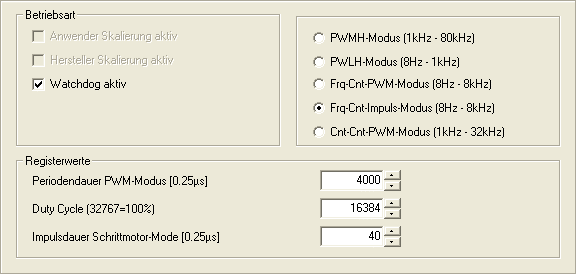
Parametrierung der KL2521
Die Grund-Frequenz 1 ist so einzustellen, dass die Klemme bei Vollaussteuerung die im jeweiligen Einsatzfall maximal nutzbare Frequenz erzeugt. Wird hier ein zu kleiner Wert eingetragen, erreicht die Achse nicht die vorgesehene Geschwindigkeit. Bei einer zu hohen Einstellung wird die Auflösung schlechter sein als es mit dieser hoch auflösenden Klemme möglich wäre. Ist dies akzeptabel, dann muss zumindest durch entsprechend eingestellte Begrenzungen sichergestellt werden, dass die Achse nicht mit einer zu hohen Geschwindigkeit verfahren wird.
Die Betriebsart der Klemme ist entsprechend der Signaldefinition des Leistungsteils einzustellen. In diesem Beispiel wird ein Richtungssignal und ein Puls erwartet.
Die Bezugsfrequenz für das in Abbildung 2 eingezeichnete Beispiel wurde mit der Formel BF = N * S / 60 berechnet. Dabei ist BF die Frequenz in Hertz, N die Drehzahl in RPM und S die Schrittzahl des Motors in der gewählten Betriebsart.
Rechenbeispiel:
BF = 1200 [RPM] * 200 [1/R] / 60 [s/min] = 4000 Hz
Das nachfolgende Beispiel zeigt die korrekte Einstellung für dieses Beispiel.
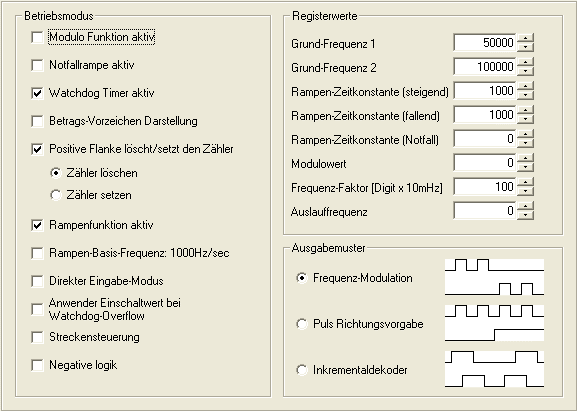
Einstellungen in der TwinCAT NC
Der Skalierungsfaktor des Encoders (Sf) ist aus dem Vorschub pro Motorumdrehung (VU) und der Schrittzahl (S) des Motors in der gewählten Betriebsart zu errechnen:
Sf = VU / S
Einsatz einer KL2521
Beim Einsatz einer KL2521 ist die Bezugsgeschwindigkeit (Vref) des Antriebs aus der Bezugsfrequenz (BF) und dem Skalierungsfaktor (Sf) des Encoders zu errechnen, die Bezugsausgabe ist hierzu auf 1.0 einzustellen. Wenn die Bezugsfrequenz der Klemme entsprechend der maximal nutzbaren Frequenz eingestellt ist kann in den Globalen Achsdaten die „Maximal erlaubte Geschwindigkeit“ und die „Eilganggeschwindigkeit (G0)“ auf maximal etwa 90% der Bezugsgeschwindigkeit eingestellt werden. Wurde die Bezugsfrequenz höher gewählt, darf maximal etwa 90% der Geschwindigkeit eingetragen werden, die sich bei exakter Einstellung der Bezugsfrequenz ergeben würde.
Vref = BF * Sf
Einsatz einer KL2502-0010 oder -3020
Kommt eine KL2502-0010 oder -3020 zum Einsatz, kann die Bezugsgeschwindigkeit des Antriebs in zwei alternativen Darstellungen eingegeben werden. Die erste Möglichkeit benutzt eine Hochrechnung der Ausgabefrequenz auf den vollen Werteumfang des Sollwerts, auch wenn diese Frequenz von der Klemme nicht dargestellt werden kann. Dabei stellt S die Schrittzahl des Motors in der gewählten Betriebsart dar. Die Bezugsfrequenz (BF) ist das Produkt des maximalen Ausgabewerts und der Frequenzskalierung und ergibt sich zu 32768*8=262144.
Vref = BF * S = 262144 * S
Alternativ kann die Bezugsgeschwindigkeit des Antriebs bei der gewählten Maximaldrehzahl vorgegeben werden. Dazu ist die entsprechende Maximalfrequenz (Fmax) und die Schrittzahl (S) des Motors in der gewählten Betriebsart zu verrechnen.
Vref = Fmax * S
Als Bezugsausgabe ist dann der zugehörige relative Aussteuerungsfaktor (A) anzugeben.
A = Fmax / BF = Fmax / 262144
Alle anderen Parameter der Achse sind in derselben Weise einzustellen wie bei einer Servo-Achse. Dabei ist insbesondere bei der Einstellung der Beschleunigung, Verzögerung und Maximal-Ruck durch empirische Tests mit der maximalen im Betrieb zu erwartenden bewegten Masse zu testen. Es darf auch hierbei nicht dazu kommen, dass die Achse wegen Überlastung einen Teil der Bewegung auslässt.