Principle of the sine/cosine measurement
A position encoder with sine/cosine interface 1 Vpp outputs two sine signals phase-shifted by 90° as analog voltages. Both signals are transmitted over two lines differentially as signal and counter signal, the voltage difference between the two lines giving the wanted signal in peak-to-peak volts. A level of 1 Vpp is usual. A full 360° cycle of the sine signal is designated as a period. Up to 10,000 periods per mechanical revolution are typical for rotary encoders.
If the rotary/linear encoder is moved, an occasionally high frequency alternating voltage is generated, which is subject to the known dynamic limits such as maximum input frequency and amplitude attenuation/level in the sequential electronics.
In extending the signal of a digital incremental encoder, which can only evaluate these full steps/cycles, the downstream circuitry can interpolate the two phase-shifted sine signals and thus determine the position n-thousand times more precisely, even within a cycle.
For the EJ5021 EtherCAT plug-in module this period resolution by interpolation is 8 ... 13 bits corresponding to 256 ... 8192-fold micro-resolution of the period.
![]() | Microincrements For the same purpose, the EJ5021 EtherCAT plug-in module uses a time-based microincrement method to also resolve digital encoder steps into up to 256 microincrements. |
In addition a Reset/C signal from the encoder can be connected in order to mark a special position, e.g. the zero position. This signal can be used for resetting or latching.
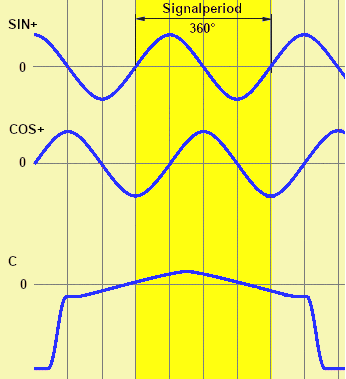